Create Purchase Order Plan
If your
Sales Forecasts contain Items that you will purchase for resale, you should run the 'Create Purchase Order Plan' Maintenance function periodically. This function will create a
Purchase Order Plan that will help you schedule the purchasing of each Item in sufficient quantities to meet the Sales Forecast and to satisfy the
Stock Policy (beginning-of-period stock level).
If you need to see a list of the Items that will be included in the Purchase Order Plan that will be created by this function together with quantities and detailed calculations, produce a Create Purchase Order Plan - Preview report.
The 'Create Purchase Order Plan' Maintenance function will create Purchase Order Plans as follows:
- It will check Sales Forecasts from the specified period for Items that need to be purchased (i.e. for Stocked Items without Recipes). Only Sales Forecasts that have been marked as OK will be checked.
- Each Stocked Item without a Recipe in Sales Forecasts will be included in its own row in the resulting Purchase Order Plan. The Needed Date for each Item will be the first day in the Sales Forecast period i.e. the first day in a week or month.
- The function will also check the Recipes used in Production Plan rows from the specified period for Items that need to be purchased (i.e. for components required by the Recipes). Again, only Production Plans that have been marked as OK will be checked. Each component that needs to be purchased will be added to the Purchase Order Plan.
Note that the Start Date in a Production Plan row will probably be outside the period of the Production Plan as a whole. The Start Date in each row (i.e. the date when production work should start) is likely to be in an earlier week or month. In deciding which components should be included in the new Purchase Order Plan, this function will check whether the Start Dates in each individual row fall in the specified period. It will not check the period of the Production Plan as a whole.
- The calculation of the required quantity for each Item in a Purchase Order Plan will take into account the quantity in the Sales Forecast (i.e. the estimated quantity that will be sold during the Forecast period), the quantity currently in stock (or estimated to be in stock at the beginning of the Forecast period) and the quantity that is required to be in stock at the end of the period (taken from the Stock Policies setting).
The calculation of the required quantity for an Item that needs to purchased because it is a component in a Production Plan will similarly take into account the quantity currently in stock (or estimated to be in stock at the beginning of the Production Plan period) and the quantity on unfulfilled Purchase Orders that is scheduled to arrive during the Production Plan period (based on the Planned Delivery Date in the Purchase Orders). This calculation will not use Stock Policies, because the Stock Policy for the finished Item will already have been used in the calculation of the quantity in the Production Plan.
- If an Item is the Produced Item in a Default Auto Production Item record, the Item from that record will be placed in the Item to Order field on flip C of the Purchase Order Plan row. This will be the case when the Item is a generic Item, and you need to be more specific when ordering from the Supplier. The Item to Order is the Item that will be included in any Purchase Orders that you create from the Purchase Order Plan.
- There may be occasions where an Item is included more than once in a Purchase Order Plan. Usually this will be because the Item is a component in more than one Recipe in a Production Plan. However, if you are using the Only for the First Order Date option in the Forecast Settings setting, such an Item will only be included once in the Purchase Order Plan, with the earliest Needed Date and quantity.
- Each Purchase Order Plan row will contain a date when the Item should be ordered, to ensure that all units will arrive by the Needed Date. Usually this Order Date will be determined by the Delivery Days in the Item's Default Purchase Item. However, you can specify that Items that will theoretically be ordered a few days apart can be ordered on the same date (using the Purchase Order Buffer Days field in the Forecast Settings setting). Please refer to the Order Dates in Purchase Order Plans page for details.
If you are using both Production Plans and Purchase Order Plans, you will usually need to create a Production Plan from a Sales Forecast, mark the Production Plan as OK, and then run the 'Create Purchase Order Plan' Maintenance function for an earlier period or periods. This is because the purchase of a component will probably need to be in an earlier period than its use in a Production. Please refer to the
Dates and Workflow page for more details.
The function will create a single Purchase Order Plan for each week or month in the period that you enter in the specification window. The duration of the Purchase Order Plan (weekly or monthly) will depend on the Period Type that you have chosen in the Forecast Settings setting. For example, if you have chosen "Months" as the Period Type and you enter a period that is six months long, six Purchase Order Plans will be created. If you have chosen "Weeks" as the Period Type, a separate Purchase Order Plan will be created for each week in the period.
If a Purchase Order Plan for a particular period already exists when you run the function, one of the following will happen:
- If you have not created Purchase Orders from the previous Purchase Order Plan (i.e. the Purch. Ord. No. field on flip C in every row is empty), it will be marked as Closed and a new Purchase Order Plan created.
- If you specified an Item, range of Items, Item Group or range of Item Groups when creating the new Purchase Order Plan, the previous Purchase Order Plan will only be closed if it includes at least one Item in the specified range or Item Group.
- Usually, any amendments that you may have made in the previous Purchase Order Plan (e.g. any Adjusted Qtys or Suppliers that you may have entered, or any rows that you may have added) will not be transferred to the new Purchase Order Plan. However, if you specified an Item, range of Items, Item Group or range of Item Groups when creating the new Purchase Order Plan, any Items in the previous Purchase Order Plan that are outside that range or do not belong to the specified Item Groups will be transferred to the new Purchase Order Plan. Any Adjusted Qtys or Suppliers etc that you entered for Items within the range will not be transferred as it will be assumed that you have entered a revised Sales Forecast for those Items, hence the need to create a new Purchase Order Plan for them.
- If you have created Purchase Orders from at least one row in the previous Purchase Order Plan, it will not be Closed and no new Purchase Order Plan will be created.
When you select the function, the 'Specify Create Purchase Order Plan' window will open:
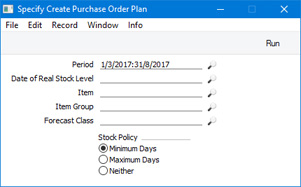
- Period
- Paste Special
Reporting Periods setting, System module
- Purchase Order Plans will be created from Sales Forecasts whose Start Dates fall within the period that you specify here, and from Production Plan rows whose Start Dates fall within this period.
- For a Purchase Order Plan to be created from a Sales Forecast, the Sales Forecast must have been marked as OK and must not be Closed. If there is more than one Version of a particular Sales Forecast, the Purchase Order Plan will be created from the latest one (with the highest Version Number) that has been marked as OK.
- Similarly, for a Purchase Order Plan to be created for a component used in the Recipe in a Production Plan row, the row must be in a Production Plan that has been marked as OK and not Closed.
- The beginning of the period must be the first day of a week (i.e. Monday) or month, depending on the Period Type that you have chosen in the Forecast Settings setting. If this is not the case, no Purchase Order Plans will be created.
- Date of Real Stock Level
- Paste Special
Choose date
- When calculating the quantity of each Item that needs to be purchased, the function will take into account the stock level at the beginning of the period, the quantity in the Sales Forecast (i.e. the estimated quantity that will be sold during the Forecast period) and the quantity that is required to be in stock at the beginning of the next week or month (taken from the Stock Policies setting).
- As it is likely that you will be creating Purchase Order Plans well in advance (so that there is sufficient time to receive the Items from the Suppliers), the period will be some time in the future and so stock levels at the beginning of the period won't be known.
- You should therefore specify here the latest date when you know the stock levels in Standard ERP are correct. From the stock levels on that date, the function will then estimate what the stock levels will be at the beginning of the period, taking intervening Sales Forecasts, Production Plans, Purchase Order Plans and Purchase Orders into account. For a Purchase Order to be taken into account, it must have a Planned Delivery Date that falls in the period specified above (it does not have to be marked as OK).
- The date that you specify here cannot be later than the beginning of the period. Ideally, the latest date is the day before the beginning of the period. If you do not specify a date, the current date will be used.
- Item
- Paste Special
Item register
- Range Reporting Alpha
- Use this field if you need to create a Purchase Order Plan for a particular Item or range of Items.
- There may be occasions when you need to replace an existing Purchase Order Plan with a new one because you changed the Sales Forecast for a particular Item. When you run this function and providing you have not already created Purchase Orders from the existing Purchase Order Plan, it will be marked as Closed and a new one created. If you specify the updated Item in this field, the other Items will be transferred from the old Purchase Order Plan to the new one. If you do not specify the particular Item here, the other Items will not be transferred to the new Purchase Order Plan, but instead they will be included based on the information in the revised Sales Forecast. This means that any Adjusted Qtys for those Items in the old Purchase Order Plan will be lost. It also means that when you revise the Sales Forecast by creating a new Version, you should keep the rows containing the Items that you don't need to update (removing an Item from the new Version of a Sales Forecast signifies that you are removing the Item from the entire purchasing process).
- Item Group
- Paste Special
Item Group register, Sales Ledger
- Range Reporting Alpha
- Use this field if you need to create a Purchase Order Plan for Items belonging to a particular Item Group or to any Item Group in a range.
- As described for the Item field above, if you specify an Item Group or Groups when creating a Purchase Order Plan when a Purchase Order Plan for the period already exists, that Purchase Order Plan will be Closed and a new one created. Items that do not belong to the specified Item Group(s) will be transferred from the previous Purchase Order Plan to the new one.
- Forecast Class
- Paste Special
Forecast Classes setting, MRP module
- If you need to create Purchase Order Plans from Sales Forecasts belonging to a particular Forecast Class, specify that Forecast Class here.
- Note that while you can use Forecast Classes in Sales Forecasts, you cannot use them in Purchase Order Plans. So, if you use Forecast Classes in Sales Forecasts, you will only be able to create a single overall Purchase Order Plan for all Classes (i.e. leave this field empty when creating the Purchase Order Plan), or a Purchase Order Plan for a single Class.
- Stock Policy
- As previously mentioned, the function will calculate the quantity of each Item that needs to be purchased. This calculation will take into account the stock level at the beginning of the period, the quantity in the Sales Forecast (i.e. the estimated quantity that will be sold during the Forecast period) and the quantity that is required to be in stock at the beginning of the next week or month (taken from the Stock Policies setting).
- The Stock Policies setting allows you to specify what the stock level for each Item should be at the beginning of each week or month. You can specify minimum and maximum figures, both expressed as a number of days' sales. Use these options to specify whether the calculation should use the minimum or maximum figures for each Item from its Stock Policy, or whether it should not use Stock Policies at all (i.e. each beginning-of-period stock level for an Item should be the full Sales Forecast figure for that period).
When the specification window is complete, click (Windows/Mac OS X) or tap (iOS/Android) the [Run] button to activate the function. The relevant Purchase Order Plan(s) will be created and placed in the Purchase Order Plan register. They will not be marked as OK, allowing you to check and amend them before going on to create
Purchase Orders to begin the ordering process.
---
Maintenance functions in the MRP module:
Go back to: