Operations Menu - Reservations
This page describes the 'Reservations' function on the Operations menu in the Sales Order record window. If you are using iOS or Android, the 'Reservations' function is on the Tools menu (with 'wrench' icon).
---
Standard ERP contains two separate methods that you can use to reserve stock for Sales Orders.
- You can use the Reserved check box on the 'Terms' card of the Sales Order record. This ensures you will always retain a sufficient quantity of the ordered Items in stock, allowing you to fulfil the Sales Order. You can use the 'Item Status' function to establish the reserved quantity of a particular Item.
- You can only use the Reserved check box to reserve Items that are in stock. If you need to reserve Items that are not in stock, you can use the Stock Reservations feature. When you enter a Sales Order, use the 'Reservations' function to reserve both existing stock and Items that are not in stock, that you have not yet ordered from their Suppliers. When you create Purchase Orders for the Items that are not in stock, and when those Items arrive, the Goods Receipt will reserve a sufficient quantity so that you can fulfil the Sales Order. The Stock Reservations feature also allows you to reserve particular Serial Numbers for an Order.
The Stock Reservations feature is described on this page. To configure such a system, follow these steps:
- In the Stock Reservations Settings setting in the Sales Orders module, select the Using Logical Stock Levels option:
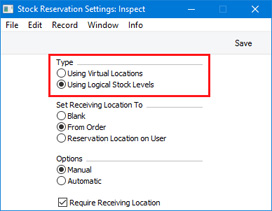 The other options in this setting are described during the illustrated example below.
- If you are using Locations, the Location in a new Sales Order will be taken from the current user's record in the Person record or from the Local Machine setting in the User Settings module.
You can also specify an Order Reserv. Location in each Person record. If you as the current user use the Reservations feature in a Sales Order, the Location in that Sales Order will change to your Order Reserv. Location if you have one. If you are also using the Reservation Access feature (point iii below), this can help prevent other sales persons from taking stock that is reserved for your Sales Orders, and to provide greater detail for reporting. Note that the Order Reserv. Location must be a real Location that can be delivered to, because it will be used in Purchase Orders.
If you change the Location or the Order Reserv. Location in a Person record, you will need to restart Standard ERP for the change to take effect. In a multi-user system, you will need to restart the server.
- An optional step is to use the Stock Reservation Access feature to specify the Locations from which each Person can remove stock. Please refer to the description of the Stock Reservation Access setting here for more details about this feature.
Having completed the configuration work described above, you can now use the Stock Reservations feature, as follows:
- Enter a Sales Order as usual.
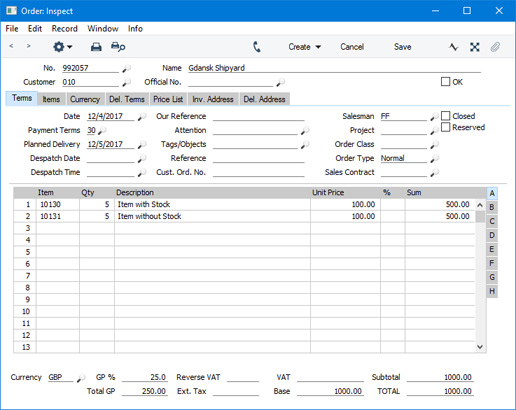 If an Item in the Order is Serial Numbered, you will need to reserve a particular Serial Number. Specify the Serial Number on flip E before proceeding to the next step. If the Item is Serial Numbered at the unit level and you have sold more than one, enter separate rows each with a Qty of 1.
If you need to reserve stock for the Order, save it and then select 'Reservations' from the Operations menu (with 'cog' icon, Windows/Mac OS X) or Tools menu (with 'wrench' icon, iOS/Android). The 'Order Reservations' report illustrated below will appear.
If you specified an Order Reserv. Location in the current user's Person record (point ii above), the Location in the Order will be changed automatically to this Order Reserv. Location before the report appears.
If you have printed an Order Status report to screen, you can also open the Order Reservations report by clicking (Windows/Mac OS X) or tapping (iOS/Android) the "Reserved" column heading in the report. The Order Reservations report illustrated below will again appear, but in this case, the Location in the Order will not be changed automatically to the current user's Order Reserv. Location:
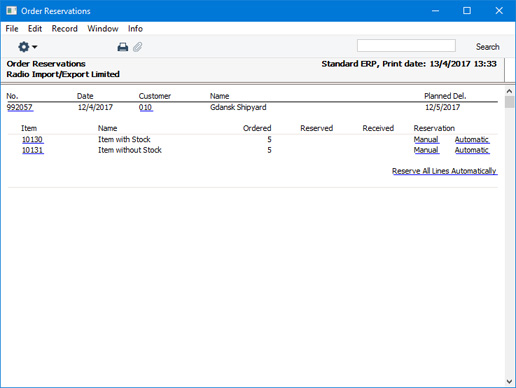 In this example, the Sales Order contains one Item that is in stock and one that is not. For the purposes of the example, we will reserve stock of the first Item while waiting for the second Item to be ordered and received.
If any Items in the Order are Serial Numbered, the Serial Numbers (from flip E of each Order row) will be listed individually.
The Order Reservations report offers three ways that you can use to reserve stock: Manual, Automatic and Reserve All Lines Automatically. If you use the Manual method, you will make decisions at each stage of the process. If you use either of the Automatic methods, these decisions will be made in the background. To be able to use the Automatic methods, you must select the Automatic option in the Stock Reservation Settings setting (point i above) (the Reserve All Lines Automatically option will not be visible if you are not using this option). In the examples below, we will use the "Manual" option to illustrate the process.
- The first Item, Item 10130, is in stock. To reserve stock of this Item against the Order, follow these steps:
- Click or tap the [Manual] text link next to the first Item in the report. A second Order Reservations report is produced, showing stock levels of the Item in each Location:
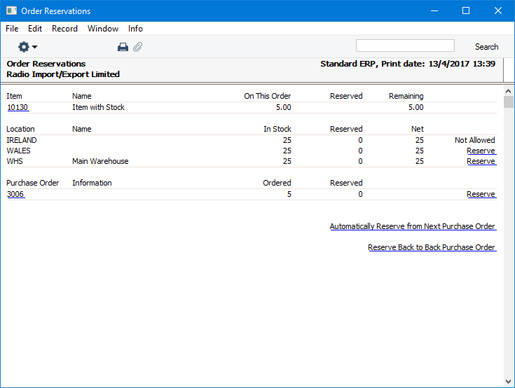 The report can contain up to three sections, as shown in the illustration:
- The first section displays details from the Order row.
- The second section displays stock in each Location. The Reserved column shows the quantity reserved for other Sales Orders, while the Net column shows the quantity that is available for reservation.
In the example above, Location IRELAND is marked as "Not Allowed" because the current user is not allowed to take stock from this Location. This is controlled using the Stock Reservation Access setting: please refer here for details.
In this example, the Location in the Sales Order is WHS. It is possible to reserve stock in other Locations, but this is not recommended. Instead, you should move stock to the Order Location before reserving it. You can do this by creating a Stock Movement from the Order (by selecting 'Stock Movement' from the Create menu).
- The third section displays open Purchase Orders for the Item (Purchase Orders where the Items have not yet been received into stock). You can reserve stock from a Purchase Order before it has arrived, but again it is recommended that you only do so from Purchase Orders issued from the same Location as the Sales Order.
- Click the [Reserve] text link next to the Location that is to supply the stock to satisfy the Sales Order (in this example, the WHS Location, the same Location as the Sales Order). A new record will be created in the Stock Reservations setting, and will be opened in a window with the title 'Stock Reservation: New', signifying that it has not yet been saved:
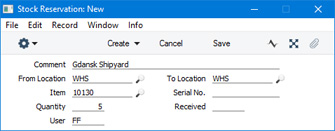 This indicates that you want to reserve a quantity of five of Item 10130 that is currently in Location WHS. The To Location: is the Location where the stock should be when it is reserved. The default in this field will be the Location in the Order.
- Save the Stock Reservation record.
- The second Item in the Order, Item 10131 is not in stock yet. You therefore need to reserve some of the Items on the next Purchase Order to be able to satisfy this Sales Order. Follow these steps:
- Returning to the Order Reservations report shown in step 2, click or tap the [Manual] text link next to the second Item, 10131. A second Order Reservations report is produced:
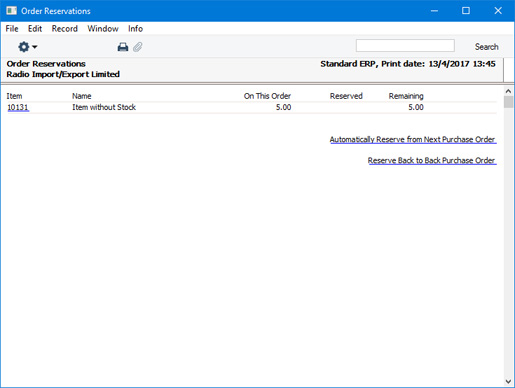
- As there is no stock and no open Purchase Orders, the report is empty apart from [Automatically Reserve from Next Purchase Order] and [Reserve Back to Back Purchase Order] text links. For this Item, click or tap the [Automatically Reserve from Next Purchase Order] button to open a second new Stock Reservation record:
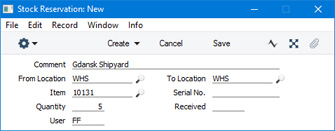
- Save the Stock Reservation. It will wait for you to create a Purchase Order containing the Item. When you approve the Purchase Order, the Purchase Order and the Stock Reservation will be connected automatically (this is described in more detail in steps 10 and 11).
- If you used the Automatic method, the process would first attempt to reserve existing stock. If there is insufficient stock to satisfy the Order, that stock would be reserved and the remaining stock would be reserved from existing open Purchase Orders. Any remaining quantity would be reserved from the next Purchase Order.
- At any time, you can check the Reservation status of the Sales Order by selecting 'Reservations' from the Operations menu:
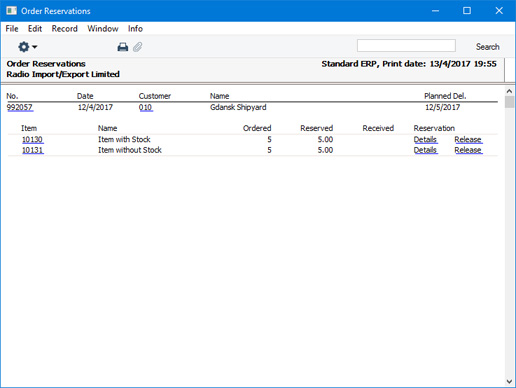 The Reserved column shows that the necessary Items are now fully reserved. As the Items have now been fully reserved, the [Manual] and [Automatic] text links have been replaced by [Details] and [Release] links. If you click or tap the [Details] links, more details about each Reservation will be shown:
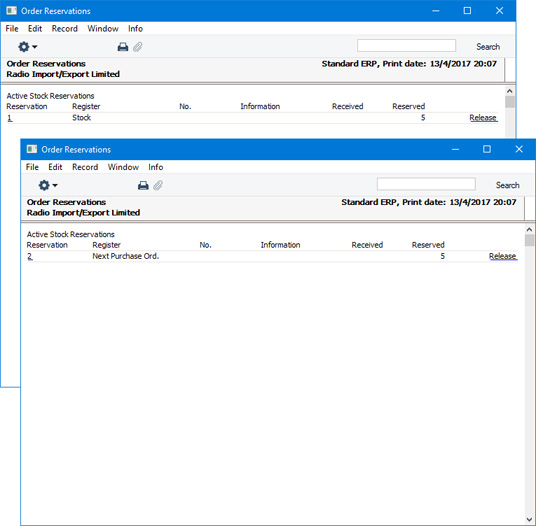 The Register column shows the nature of each reservation, from stock and from the next Purchase Order respectively.
Each reservation is in fact a record in the Stock Reservations setting. You can open these records by drilling down from the Reservation Number in the reports (left-hand column), or you can open them directly from the setting:
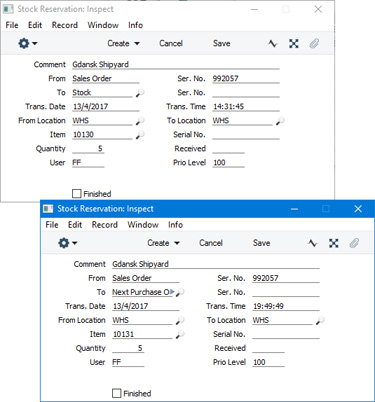 The To field shows the nature of each Reservation. In the Stock Reservation record for the Item that is in stock, this field contains "Stock", and in the Stock Reservation record for the Item that is not in stock it contains "Next Purchase Order".
- If the Sales Order Quantity increases, use the 'Reservations' function as already described to reserve the extra quantity.
- If the Sales Order Quantity decreases, you will be told "Reserved quantity is higher than ordered quantity, please update the reservations accordingly" when you try to save the Order. Cancel the changes to the Order, then select 'Reservations' from the Operations (Windows/Mac OS X) or Tools (iOS/Android) menu and use the [Release] text link for the relevant Item(s) to remove the reservations. This will delete the relevant records from the Stock Reservations setting. Reduce the Quantity in the Order, save the Order and then use the 'Reservations' function to reserve once again.
- If you need to remove a reserved Item from the Sales Order or change to a different Item, you must first find and delete the Stock Reservation record. To do this, you can use the 'Reservations' function and the [Release] text link as described in the previous step. An alternative method (which you can also use in the previous step) is to find the relevant record in the Stock Reservations setting, open it and select 'Release Reservation' from the Operations or Tools menu.
- Enter a Purchase Order for the Item that is not in stock in the usual way. You can enter it directly to the Purchase Order register, or you can use the 'Purchase Order' (Create menu or Maintenance functions.
- Mark the Purchase Order as OK and save it. The Purchase Order Number will be copied to any "Next Purchase Order" Stock Reservation records for the Item/Location combination, and the To field in those records will be changed from "Next Purchase Order" to "Purchase Order". This connects the Stock Reservations to the Purchase Order:
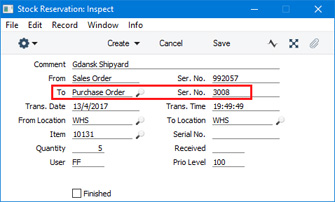 If the Purchase Order Quantity is not sufficient to satisfy all the "Next Purchase Order" Stock Reservation records for the Item/Location, only the earliest Stock Reservation records will be connected to the Purchase Order. If necessary, a Stock Reservation record will be divided into two, so that a partial quantity can be connected to the Purchase Order. A second Stock Reservation record will be created, allowing the remaining quantity to retain the "Next Purchase Order" status, waiting for the next Purchase Order.
If a Stock Reservation is not connected to a Purchase Order as described and when expected, the probable reason is that the Location in the Purchase Order is not the same as the To Location in the Stock Reservation.
You must mark a Purchase Order as OK and save it in order for it to be connected to a Stock Reservation. As this is a vital part of the reservation process, you will not be able to create a Goods Receipt from any Purchase Order that has not been marked as OK if there are any "Next Purchase Order" Stock Reservations. This will ensure that this step is not forgotten.
- The Operations/Tools menu of the Purchase Order has its own 'Reservations' function. After you have marked the Purchase Order as OK and saved it, you can use this function to see whether any of the Items on the Purchase Order have been "pre-reserved" (reserved before they have arrived in stock):
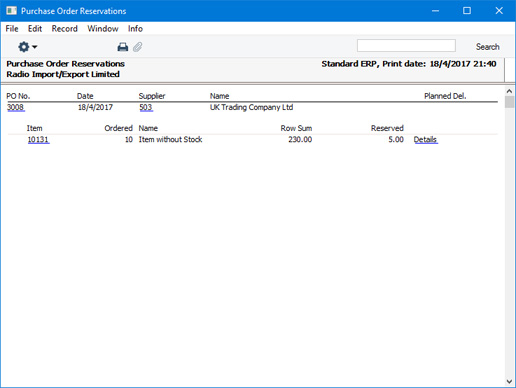 Click or tap the [Details] text link to see the Sales Orders for which the Items have been reserved:
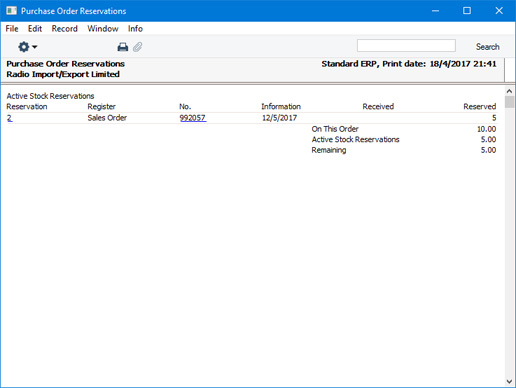 You can open a Sales Order or a Stock Reservation record from this report by drilling down.
- When the goods arrive in stock, create a Goods Receipt from the Purchase Order in the usual way. The Goods Receipt will contain separate rows for each connected "Purchase Order" Stock Reservation, and one for the remaining quantity:
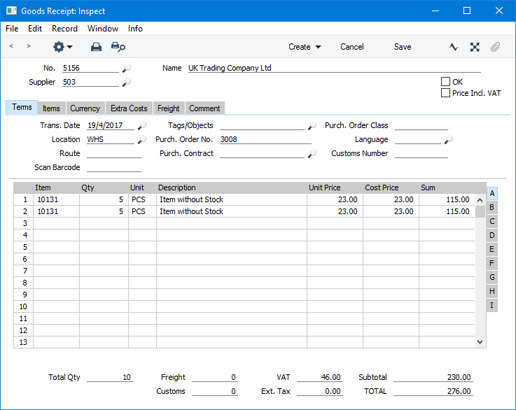
- Mark the Goods Receipt as OK and save it to bring the Items into stock. The connected "Purchase Order" Stock Reservation record will be marked as Finished and a new "Stock" Stock Reservation record will be created, containing the Goods Receipt Number. The quantity received will be placed in the Received field in both records:
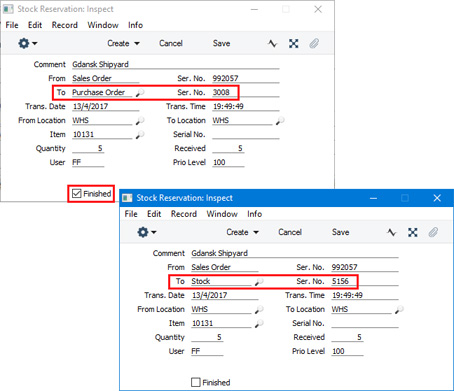 If you did not receive the full Purchase Order Quantity, change the Quantity in any Goods Receipt row, as normal. If you change the Quantity in a row that receives stock against a Stock Reservation, the result will be that the Received figure in the connected "Purchase Order" Stock Reservation record will be less than the Quantity. The Stock Reservation will therefore remain open, waiting for the next Goods Receipt with the remaining Purchase Order Quantity. A "Stock" Stock Reservation will still be created for the quantity that you did receive.
- From the Sales Order, you can use the 'Reservations' function to monitor when the reserved Items arrive in stock. In the example, the Received column in the 'Order Reservations' report will now show that the five reserved units of Item 10131 are in stock:
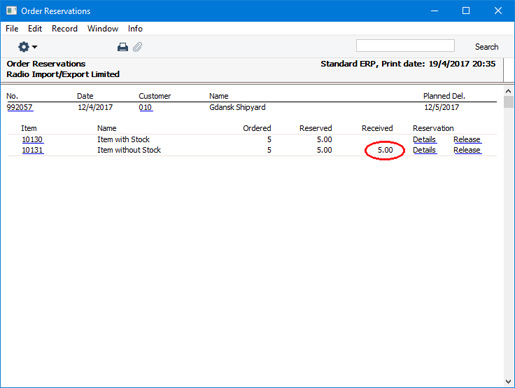 - The reserved quantity will be reflected in the 'Item Status' window (Reserved = Stock - Not Reserved):
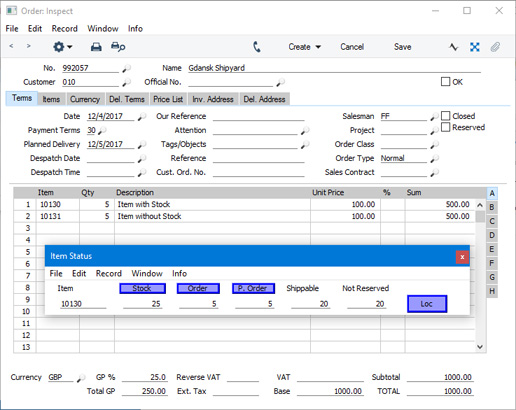 If you enter an Order for an Item that has a quantity reserved for an earlier Order and then create a Delivery from the new Order, the Avail. figure in that Delivery will not include the reserved quantity. In the example, the Avail. quantity in a new Delivery for Item 10130 will be 20.
- Once the Items are in stock, you can issue a Delivery from the Order in the usual way, by selecting 'Delivery' from the Create menu. When you mark the Delivery as OK and save it, the Stock Reservation records will be marked as Finished:
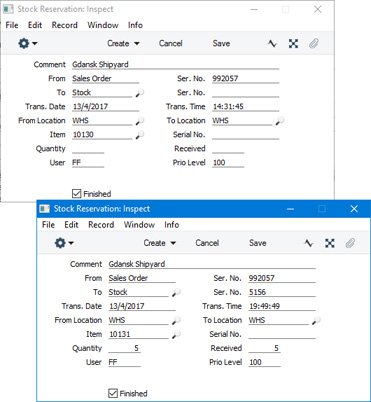 Stock Reservation records will not be marked as Finished if the Delivery is only partial. When you make the final Delivery, all relevant Stock Reservation records will be marked as Finished.
---
The Sales Order register in Standard ERP:
Go back to:
|