The Recipe Register - Row Fields
This page describes the fields in the matrix in the Recipe window. Please refer here for an introduction to the register and for descriptions of the fields in the header.
---
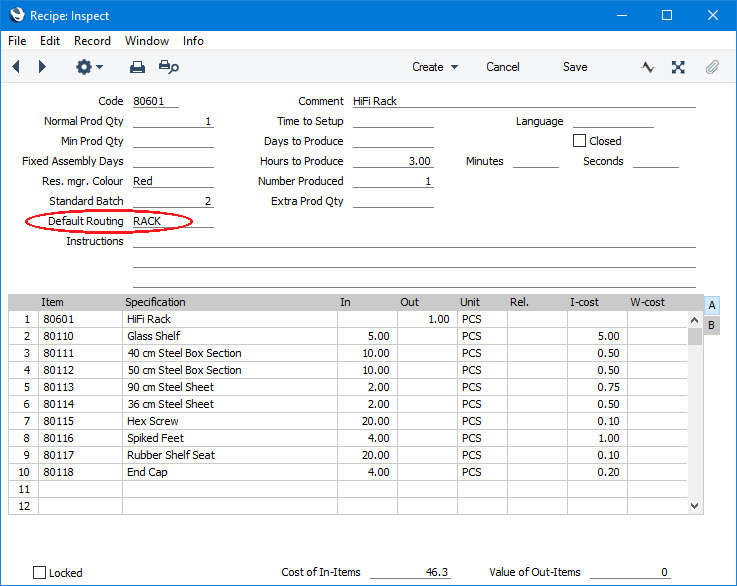
Use the grid area that takes up most of the screen to list the Input Items (i.e. the components that will be used to build the final assembly) and to specify the Item Number of the assembly or the finished product (i.e. the result of the Recipe). This must be a Structured Item or a Stocked Item. If you will use the Production register to build the Item, or if the result of the Recipe will itself be used as a component in another Recipe, it must be a Stocked Item. A Recipe can result in more than one assembly or finished product: if so, they should all be the same Type (i.e. all Structured Items or all Stocked Items).
Flip A- Item
- Paste Special
Item register
- Enter the Item Numbers of each of the Input Items (i.e. the components) and of the Output Item(s) (i.e. the finished product). You can list the Items in any order.
- You cannot use Structured Items as components.
- If you need a Recipe to contain costs such as electricity, labour, etc as components, these costs should be Plain or Service Items. Use Service Items in which the Cost Price is blank if you need to be able to enter different cost values in each Production, or Service Items with a Cost Price or Plain Items if you need standard cost values. The I-Cost of a Plain or Service Item in a Production will be copied from the Cost Price field in the relevant Item record each time you save the Production, with the exception that the I-Cost will not be updated if the Item is a Service Item and the Cost Price is blank.
- You can use an Item with Varieties as a component or as a finished Item. You must enter the combined Item/Variety Number (i.e. you must choose a specific Variety). Use 'Paste Special' from this field or from the In or Out Qty fields to ensure the combined Number is correct. Please refer here for more details about Varieties.
- In addition to the 'Paste Special' feature, you can use the 'Item Search' function on the Operations menu (Windows/macOS) or Tools menu (iOS/Android) to add Items to the Recipe.
- If the Recipe is one you will use in a Production Order and you will work on the resulting Productions using the Production Time Entry interface, the Recipe cannot contain any Serial Numbered Items. The Production Time Entry interface is simplified to the extent that Serial Numbers cannot be registered.
- Specification
- The Item Name from the Item register will be placed here when you enter the Item Number.
- In
- Enter the quantity of each component required to make or build the finished product. Do not enter an In quantity for the assembled Item(s).
- If an Item is Serial Numbered at unit level, you can enter the full required In Quantity. When you use the Recipe in a Production, the Production will contain the appropriate number of rows each with an In Qty of one, allowing you to enter Serial Numbers individually.
- In any Nominal Ledger Transactions arising from Production records using this Recipe, the credit amount will be taken from the rows with an In Qty (i.e. Input Items).
- Out
- This field contains the quantity of assembled Items that can be made from the components listed above. Usually, this will be just one, and it must be one if the Out Item is a Structured Item.
- If an Item is Serial Numbered at unit level, you can enter the full required Out Quantity. When you use the Recipe in a Production, the Production will contain the appropriate number of rows each with a Out Qty of one, allowing you to enter Serial Numbers individually.
- In any Nominal Ledger Transactions arising from Production records using this Recipe, the debit amount will be taken from the rows with an Out Qty (i.e. Output Items).
- Rel.
- Relativity. You must use this field if the result of the Recipe is that more than one Item will be assembled (i.e. there is more than one row in the Recipe with an Output Item). Enter a figure in each row representing an Output Item. When you mark a Production using this Recipe as Finished, the total stock value of the Input Items will be calculated using the appropriate Cost Models. The stock values of the Output Items will then be calculated from that total using the ratio that you enter here.
- The Relativity figures are not percentages but ratios. For example, the total stock value of the Input Items is 103 and there are two Output Items with Relativities of 30 and 60 respectively. The stock value of the first Output Item will be 103 * 30/(30 + 60), and the stock value of the second Output Item will be 103 * 60/(30 + 60). If the Out Qty of the first Output Item is two, then the unit stock value of the first Output Item will be 103 * 30/((2*30) + 60), and the stock value of the second Output Item will be 103 * 60/((2*30) + 60).
- If the Recipe has more than one Output Item, you will not be able to save it if you have not specified a Relativity figure in every row with an Output Item.
- I-cost
- The cost value (per unit) of the component or assembled Item. If the row contains an Input Item, enter the unit Cost Price for the Item. The default will be the Cost Price of the Item. The cost shown in this field is NOT the same as the stock value calculated using the usual Cost Model. You can update this figure to the latest Cost Price in the Item record using the 'Update Recipes' Maintenance function.
- If the row contains an Output Item (i.e. the assembled Item), enter the unit cost value of that Item. This will usually be the sum of the Cost Prices of the Input Items, taking quantities into account. Again, the default will be the Cost Price of the Item, and again you can update the figure using the 'Update Recipes' function. In this case, however, 'Update Recipes' will change the figure to the latest sum of the Cost Prices of the Input Items, and optionally will copy this new sum figure to the Cost Price field in the Item record for the assembled Item.
- The total Input Costs are shown in the Cost of In-Items field in the footer, while the total Output Costs are shown in the Value of Out-Items field.
- W-cost
- The W-cost is the Work Cost incurred in building or assembling the Recipe. Usually, this will be cost of the labour required to build the assembled Item.
- You should only specify a Work Cost if the result of the Recipe is a Stocked Item that you will build using the Production register. If the result is a Structured Item, the Work Cost will be ignored.
- You should enter the Work Cost in a row featuring an Input Item, as shown on the illustration above. This ensures the Work Cost will correctly be credited to the Production Work Cost Account in any Nominal Ledger Transactions arising from Production records using this Recipe. If you enter the Work Cost in an Output row, the Work Cost will incorrectly be debited (not credited) to the Production Work Cost Account.
- You can usually place the Work Cost in any Input row, but do not enter it in a row in which the Input Item is a Service Item. However, you may need to choose the row more carefully if you are using the Use Item Groups for Cost Accounts option in the Cost Accounting setting in the Stock module and you have specified Production Work Cost Accounts in your Item Groups. In this situation, the Production Work Cost Account will be taken from the Item Group to which the Item in the row with the Work Cost belongs. You should therefore enter the Work Cost in the correct row in the Recipe, so that the correct Account will be credited. If you are not using the Use Item Groups for Cost Accounts option or you have not specified a Work Cost Account in the relevant Item Group, the Production Work Cost Account will be taken from the Account Usage Stock setting.
- Although you should enter the Work Cost in an Input row, the figure is independent of the In Qty in that row. For example, if the Work Cost is 10.00, enter 10.00: do not enter 5.00 if the In Qty is 2.
- The Work Cost should be the total cost incurred through one application of the Recipe. For example, if the Out Qty of the assembled Item is 2, this means that one application of the Recipe will add two assembled Items to stock. If the cost incurred in assembling these two Items is 10.00, enter 10.00 as the Work Cost. Do not enter the cost per unit, 5.00.
- If you are using the Add Work Cost option in the Production Settings setting, a Work Cost will be added to the Recipe automatically. This Work Cost will be calculated using the Work Cost per Hour specified in the same setting and the time required for the Recipe (the total of the Time to Setup and the Days, Hours, Minutes and Seconds to Produce). The Work Cost will be placed in the W-cost field in the last Input row in the Recipe. You cannot change this calculated Work Cost figure: if you need to adjust it, add a Plain or Service Item to the Recipe with an In Qty and appropriate I-Cost (use Service Items in which the Cost Price is blank if you need to be able to enter different cost values in each Production, or Service Items with a Cost Price or Plain Items if you need standard cost values. The I-Cost of a Plain or Service Item in a Production will be copied from the Cost Price field in the relevant Item record each time you save the Production, with the exception that the I-Cost will not be updated if the Item is a Service Item and the Cost Price is blank).
- Work Cost values are included in both the Cost of In-Items and Value of Out-Items fields in the footer.
- You cannot enter a Work Cost if the Recipe has a Routing (the automatic addition of a Work Cost controlled by the Add Work Cost option will not occur in this situation). If a Recipe has a Routing, you should record the Work Costs either by specifying times in each Standard Operation or using Activities Please refer to the description of the Time options (Actual and Fixed) in the Productions Settings setting for more details. An alternative would be to use Plain or Service Items as previously described.
Flip B- Description
- Use this field to record notes about the Item and its use in the Recipe.
- Material
- Paste Special
Materials setting, Production module
- If the Recipe has a Routing (i.e. it represents a Production process that has been divided into stages), you should assign a Material to each Input and Output Item (unless an Input Item is a Plain Item with its own Recipe, in which case you should leave this field empty and assign Materials in that Recipe).
- The Material is the mechanism that connects each Item to a stage (i.e. to an Operation) in the process. In the case of an Input Item, the Material determines the stage in the process when it will be removed from stock. In the case of an Output Item, the Material determines when the completed Item will be added to stock.
- Please click here for more details and an example.
- Recipe
- This field shows whether the Item is an assembly (i.e. it has a Recipe specified on its 'Recipe' card). This is updated automatically and can't be changed.
Footer- Locked
- Once you are certain the Recipe is correct, you should check this box to prevent further changes. Once you have used a Recipe in a transaction (e.g. Delivery or Production), you should not change it, especially if the result of the Recipe is a Structured Item in which you have not selected the Paste Components During Entry option. In this case, changing the Recipe will introduce inaccuracies into the stock records, so the Recipe will be marked as Locked automatically when you use it in a Delivery for the first time. However, before the Delivery stage is reached and before even using such a Structured Item in a Sales Order, it is recommended that you lock its Recipe yourself. Otherwise, if you include the Item in a Sales Order and then change the Recipe, the 'Order' figures (quantities on unfulfilled Sales Orders) for the components in the 'Item Status' window (and many reports) will become incorrect.
- If it subsequently becomes necessary to change a Recipe, you should not do so. Instead you should create a new one (and attach it to a new Stocked or Structured Item).
! | Do not change a Recipe once it has been used in a stock transaction. | |
- Cost of In-Items
- This field contains the sum of the Input Costs of the Input Items (W-cost + (I-cost x In Qty)). If the assembled Item is a Stocked Item, you should transfer this value to the Cost Price field on the 'Costs' card of the Item record for the assembled Item, either manually or using the 'Update Recipes' Maintenance function in the Production module. This will ensure that gross margin calculations are correct when you sell the assembled Item.
- Value of Out-Items
- This field contains the sum of the costs of the Output Items.
---
The Recipe register in Standard ERP:
Go back to:
|