Batch Quality Control
This page describes the Batch Quality Control setting in the Service Orders module.
---
Standard ERP allows you to control the sale of perishable goods and of goods that require quality control testing. This control can be on one of two levels:
- You can control the sale of Items based on their Best Before Dates.
- You can control the sale of Items using quality control tests.
In both cases, you will specify at the Serial Number level whether a unit or batch can be sold (i.e. whether its Best Before Date has passed, or whether it has passed the quality control tests). You can therefore only use these controls with Items that have Serial Numbers at the unit or batch level.
When you need to specify whether a unit or batch can be sold, you will enter a record for that unit or batch in the Batch Quality Control setting in the Service Orders module. In this Batch Quality Control record, you should enter a Best Before Date and/or the results of the quality control tests, and you should also specify a Batch Status. The Batch Status will control whether the unit or batch can be sold.
A Batch Status can have one of three statuses:
- No Message
- The unit or batch can be sold or otherwise removed from stock freely.
- Give Warning
- A warning will be shown when you try to sell the unit or batch or otherwise remove it from stock, but you will be able to proceed.
- Disallow Use
- You will not be able to sell the unit or batch or, in some circumstances, remove it from stock (you will be able to remove it from stock using a Stock Depreciation or Returned Goods to Supplier record).
On this page, we will describe using the Batch Quality Control setting with Best Before Dates and then with quality control tests.
Batch Quality Control records and Best Before DatesIf you need to control the sale of Items with Best Before Dates, you can use the Batch Quality Control setting to determine when these Items can be sold.
An example cycle might include the following stages:
- When you receive an Item with a Best Before Date into stock, you might immediately enter a Batch Quality Control record that will allow you to sell the Item freely. You should therefore assign a "No Message" Batch Status to the Batch Quality Control record.
When you receive the Item into stock, you can specify a Best Before Date and a Batch Status in the Goods Receipt row (flip B). If you specify a Batch Status, a Batch Quality Control record will be created automatically when you mark the Goods Receipt as OK and save. The Batch Quality Control record will be marked as OK automatically, meaning that it has been activated.
You can also use a more manual method to create the Batch Quality Control record, by highlighting the relevant row in the Goods Receipt and then selecting 'Quality Control' from the Row menu (Windows/macOS) or Tools menu (iOS/Android). If you received the Item into stock using a Production or Production Operation, you must use this more manual method to create the Batch Quality Control record, as it is not possible to specify a Batch Status in a Production or Production Operation row. You can also enter the Batch Quality Control record directly to the Batch Quality Control setting in the Service Orders module.
- As the Best Before Date approaches, you might enter a second Batch Quality Control record with a "Give Warning" Status.
You can use the Best Before List report in the Stock module to find units and batches with Best Before Dates in a particular period.
If you have many Items with the same Best Before Date, you can create new Batch Quality Control records in batches using the 'Batch Status Change' Maintenance function in the Service Orders module.
- Finally, when the Best Before Date has passed, you might enter a third record with a "Disallow Use" Status. This will prevent further sales of Items belonging to the batch.
If you will use Batch Quality Control records with Best Before Dates, enter information as described below the illustration. If you create a Batch Quality Control record from another record (e.g. from a Goods Receipt), many of the fields will be filled in automatically:
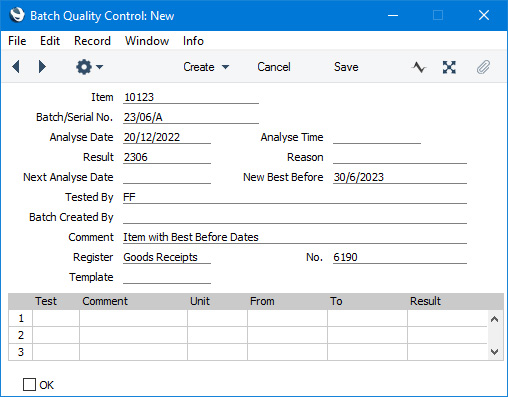
- Item
- Paste Special
Item register
- Enter the Item Number of the Item here.
- Batch/Serial No
- Paste Special
Serial Numbers of Items in stock
- Enter the Serial Number of the Item or batch of Items. Note that you can only use existing Serial Numbers (i.e. Serial Numbers that originated in the Goods Receipt, Production or Production Operation registers.
- Analyse Date
- Paste Special
Choose date
- The date of the Batch Control record i.e. the date when you checked the unit or batch.
- If you have entered several Batch Quality Control records for the same Item/Serial Number combination, the record with the latest Analyse Date will used to issue a warning on sale, or to prevent sale altogether.
- Analyse Time
- Paste Special
Current time
- The time when you checked the unit or batch.
- Result
- Paste Special
Batch Status setting, Service Orders module
- Use this field to connect the Batch Quality Control record to a record in the Batch Status setting. After you mark the Batch Quality Control record as OK and save, this Batch Status record will determine whether you will be warned when using the Item/Serial Number combination in an outgoing stock transaction, or whether you will be prevented from using the Item/Serial Number altogether.
- If you would like the latest Batch Status to be shown in the 'Paste Special' list opened from any Serial Number field, select the Show Batch Status option in the Item Settings setting in the Sales Ledger.
- Reason
- Paste Special
Standard Problems setting, Sales Ledger/Service Orders module
- Specify here a Standard Problem to describe the result of the quality control test.
- Next Analyse Date
- Paste Special
Choose date
- If the Item is one that need to be tested periodically until it is sold, enter the date of the next test here.
- New Best Before
- Paste Special
Choose date
- Enter a new Best Before Date here if necessary.
- When you mark the Batch Quality Record as OK and save, this date will be copied to the record for the Item/Serial Number in the Batch Specifications setting in the Stock module (if there is no Batch Specification record for the Item/Serial Number, one will be created automatically). From there, it will become the new Best Before Date for the Item/Serial Number. When you deliver the Item/Serial Number, this Best Before Date will be copied to the Delivery. If you leave this field empty, the Batch Specification record will not be updated so the previously recorded Best Before Date will remain valid.
- If you would like the Best Before Date to be shown in the 'Paste Special' list opened from any Serial Number field, select the Show Best Before Dates option in the Item Settings setting in the Sales Ledger.
- Tested By
- When the Batch Quality Control record is first created, the Signature of the current user will be placed here automatically and cannot be changed.
- You will only be able to mark the record as OK if your Signature is included in this field. If you are not the creator of the record, you can add your Signature by saving any changes and then selecting 'Sign Tested By' from the Operations menu (Windows/macOS) or Tools menu (iOS/Android).
- Batch Created By
- Paste Special
Person register, System module and Global User register, Technics module
- Enter the Signature of any other user connected with the Batch Quality Control test. You can enter the Signatures of more than one user, separated by commas. This is for information only.
- Comment
- Record any further notes about the Batch Status Control record here.
- If the Batch Quality Control record was created from another record (e.g. a Goods Receipt), the Item Description will be placed in this field.
- Register, No.
- If the Batch Quality Control record was created from another record (e.g. a Goods Receipt), the register and No. of that record will be shown in these fields.
- OK
- Check this box to approve the Batch Quality Control record. After you have saved it, you will no longer be able to make any changes.
- Marking a Batch Status Control record as OK and saving will also activate that record. This means that from that moment the Batch Status record quoted in the Result field will determine whether you will be warned when selling the Item/Serial Number, or whether you will be prevented from selling the Item/Serial Number altogether. The record will replace any earlier Batch Quality Control records in this role.
- You must save the record before you can tick the OK box. You will then only be able to tick the OK box if your Signature is included in the Tested By field. If your Signature is not in the Created By field, you can add it by saving the record and then selecting 'Sign Tested By' from the Operations menu (Windows/macOS) or Tools menu (iOS/Android). You should then save the record again, then tick the OK box.
- You can prevent particular users from ticking the OK box in Batch Quality Control records using Access Groups. To do this, deny them access to the 'Sign Quality Control' Action. This will also prevent those users from using the 'Sign Tested By' function.
- If you need to see a list of Batch Quality Control records that have not yet been marked as OK, run the Batch Quality Control Tests report in the Service Orders module. A similar report, Batch Quality Control Results, lists Batch Quality Control records that have been marked as OK.
Batch Quality Control records and Quality Control TestsIf you need to control the sale of Items using Quality Control Tests, you can use the Batch Quality Control setting to record the results of the tests and to determine when these Items can be sold. To make full use of this feature, you should first list the tests in the Batch Quality Control Tests setting, grouped the tests together to form Batch Quality Control Templates and specified which Template should be used for each Item/Location/Register combination using the Batch Quality Control Rules setting .
When you receive an Item that requires a quality control test into stock or use it in another stock transaction, you can create a Batch Quality Control record from the stock transaction by selecting the row containing the Item/Serial Number and selecting 'Quality Control' from the Row menu (Windows/macOS) or Tools menu (iOS/Android).You can also enter a Batch Quality Control record directly to the Batch Quality Control setting in the Service Orders module.
If you created the Batch Quality Control record from a stock transaction, the new record will be opened in a window entitled 'Batch Quality Control: New'. This means that the record has not been saved:
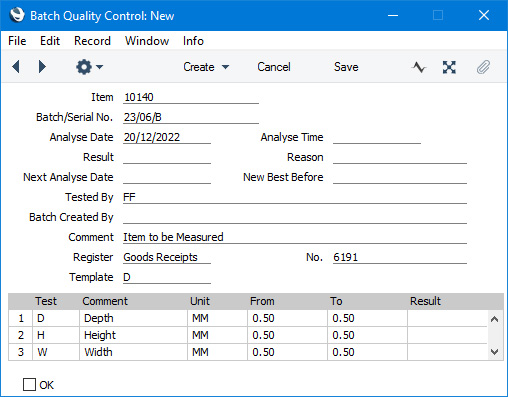 Template
Paste Special Batch Quality Control Templates setting, Service Orders module
When you specify a Batch Quality Control Template, the Tests listed in the Template will be brought in to the matrix below.
If you created the Batch Quality Control record from a stock transaction, a Template will be brought in automatically, chosen as follows:
- If there is a row in the Batch Quality Control Rules setting for the Item/Location/Register combination, the Template in that row will be used.
- If there is a row in the Batch Quality Control Rules setting for the Item//Register combination in which the Location is blank, the Template in that row will be used.
- If there is a row in the Batch Quality Control Rules setting for the Item in which the Location or the Register is blank, the Template in that row will be used.
Matrix
When you specify a Template in the field above, the Tests listed in that Template will be listed here automatically. You can also add tests yourself, using 'Paste Special' from Test field.
Enter the numeric results of the tests in the Result column.
If you need to see previous test results for the Item/Serial Number, choose 'Batch Quality Control Results' from the Row menu (Windows/macOS) or Tools menu (iOS/Android). This will print a Batch Quality Control Results report to screen. In this report, select 'Reopen Report Specification' from the Operations menu and choose the Detailed option to see the full results.After you have entered the results of the tests in the Result column in the matrix, you should then enter an overall Result in the header. As described in the 'Batch Quality Control records and Best Before Dates' section above, this Result should be a Batch Status that will determine whether you will be warned when using the Item/Serial Number combination in an outgoing stock transaction, or whether you will be prevented from using the Item/Serial Number altogether.
Again as previously described, ensure your Signature is in the Tested By field or add it by saving any changes and then selecting 'Sign Tested By' from the Operations menu (Windows/macOS) or Tools menu (iOS/Android). Save the record again, then tick the OK box and save again to activate the Batch Quality Control record. Access to the 'Sign Tested By' function and the OK box is governed by the 'Sign Quality Control' Access Group Action.
Controlling Outgoing Stock Transactions using Batch Quality Control recordsWhen you enter a Serial Number in an outgoing stock transaction (e.g. a Delivery), the Batch Quality Control setting will be checked for the latest record (determined by Analyse Date) with that Serial Number that has been as OK. If this Batch Quality Control record has a "Give Warning" or "Disallow Use" Batch Status, the Warning/Info from the related Batch Status record will be displayed:
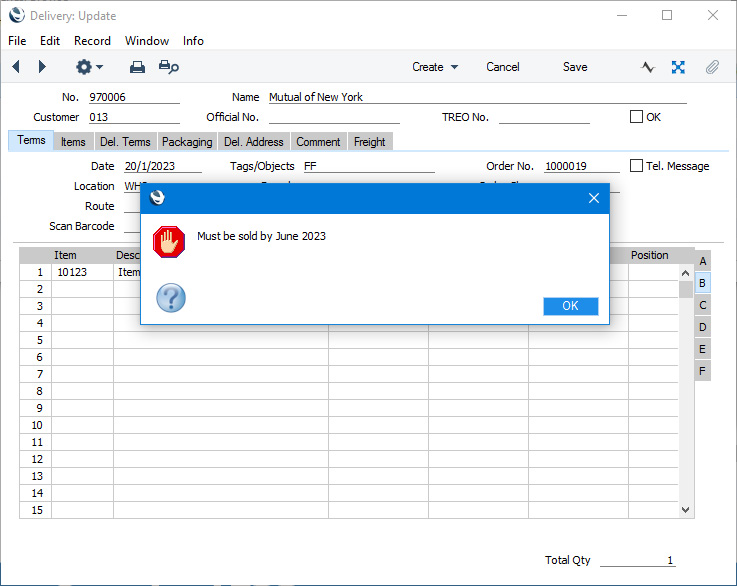 If the Batch Quality Control record has a "Disallow Use" Batch Status, you will not be able to save the transaction without changing the Serial Number.
If you are using Best Before Dates and the outgoing stock transaction is a Delivery, the correct Best Before Date will be brought in. This will be the Best Before Date specified in the Batch Quality Control record or in the original Goods Receipt. To help choose Items on the basis of their Best Before Date, you can have Best Before Dates shown in the 'Paste Special' list opened from any Serial Number field. To do this, select the Show Best Before Dates option in the Item Settings setting in the Sales Ledger. The Show Batch Status option in the same setting will cause the latest Batch Status to be shown in the 'Paste Special' list as well. If the latest Batch Status has been marked as "Disallow Use", the Serial Number will not be shown in the 'Paste Special' list. The example 'Paste Special' list below shows the Serial Number ("17/06/A"), the quantity of the batch still in stock (10), the Best Before Date and the latest Batch Status:
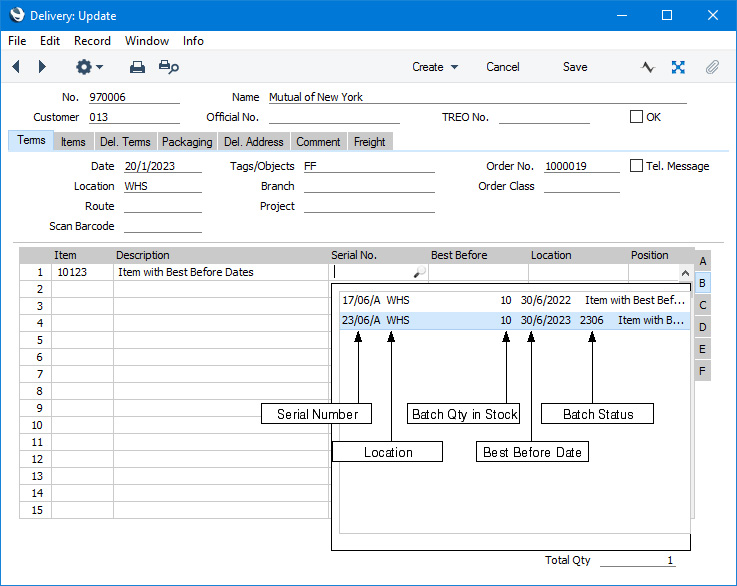
The 'Batch Status Change' Maintenance functionAs described above, the Batch Status specified in the latest Batch Quality Control record for a particular Serial Number will determine whether you can remove that Serial Number from stock and if so whether a warning will be issued. As you cannot change a Batch Quality Control record that has been marked as OK, you will need to create a new Batch Quality Control record if you need to change the Batch Status of a particular Serial Number. If you need to change the Batch Status of several Serial Numbers, you can create new Batch Quality Control records in batches using the 'Batch Status Change' Maintenance function in the Service Orders module.
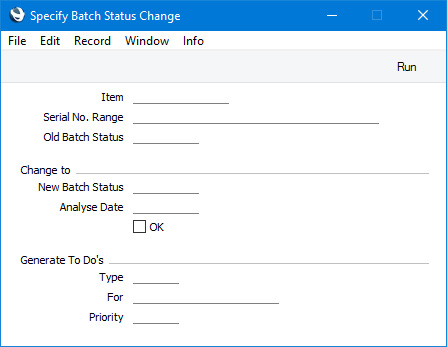
- Item
- Paste Special
Item register
- Specify the Item for which you want to create new Batch Quality Control records.
- Serial No. Range
- Range Reporting
Alpha
- Specify the Serial Number (or range of Serial Numbers separated by a colon) for which you want to create new Batch Quality Control records.
- If you leave this field empty, new Batch Quality Control records will be created for every Serial Number, including those that have already been sold. This can be useful in certain situations, for example where a product is one that is continually being updated. Each time there is a new update, create a new Batch Status record and then run this function. Use the fields at the bottom of the window to create To Do Activities that you can then use as a call list to call existing Customers about the update. Customer information will be copied from the Known Serial Number register to the new Activities. One Activity will be created for each new Batch Quality Control record, so this feature will be of most use with Unit Serial Numbers rather than Batch Serial Numbers.
- Beware of entering Serial Numbers in this field without specifying an Item Number in the field above. Doing so will have the same result as leaving both fields empty: new Batch Quality Control records being created for every Serial Number both in stock and sold.
- Old Batch Status
- Paste Special
Batch Status setting, Service Orders module
- If the purpose of creating the new Batch Quality Control records is to copy old ones, enter the Batch Status (i.e. the Result) of the Batch Quality Control records that are to be copied. The Batch Quality Control records will only be copied if they have been marked as OK.
- New Batch Status
- Paste Special
Batch Status setting, Service Orders module
- Specify here the Batch Status (Result) that is to be used in the new Batch Quality Control records. You must enter a New Batch Status, otherwise the function will have no effect.
- Analyse Date
- Paste Special
Choose date
- Specify here the Analyse Date that is to be used in the new Batch Quality Control records. You must enter an Analyse Date, otherwise the function will have no effect.
- OK
- Check this box if you want the new Batch Quality Control records to be marked as OK immediately.
- Note that this function does not place Best Before Dates in the new Batch Quality Control records. Depending on circumstances, you may want to enter Best Before Dates before marking the new records as OK.
- Selecting this option will have no effect if the Person running the function has been denied access to the 'Sign Quality Control' Action, as described earlier on this page.
- Type
- Paste Special
Activity Types setting, CRM module
- If you want the function to create an Activity for each new Batch Quality Control record, specify here the Activity Type that is to be used in the new Activities. No Activities will be created if you do not specify an Activity Type.
- Creating an Activity for each new Batch Quality Control record is useful in two circumstances. First, the product might be one that is being continually updated as described above and you want to create a To Do list of Customers to call about the update. Second, you are not marking the Batch Quality Control records as OK immediately and you want to notify the appropriate Person that this task needs to be done.
- Many details will be copied from the New Batch Status record to each new Activity. The Warning/Info of the New Batch Status will be copied to the Text field in the header, and the four lines of Comment in the New Batch Status will be copied to the 'Text' card. In the case of Serial Numbers that have been sold, Customer details will be copied to the new Activities from the Known Serial Number register. This requires you to be using the Update Known Serial Number Register option in the Stock Settings setting, which makes sure the Known Serial Number register is updated whenever an Item with Serial Numbers is sold.
- The Task Type of each new Activity will be To Do and the Symbol will be Other. The Start Date will be the Analyse Date specified in the field above, and the Start Time will be the current time.
- Each new Activity will be connected to the Batch Quality Control record from which it was generated, through its Link Manager. When viewing an Activity, you will be able to open the connected Batch Quality Control record by opening the Link Manager and following the link from there.
- For
- Paste Special
Person register, System module
- If you want the function to create an Activity for each new Batch Quality Control record, specify here the Person (or Persons, separated by commas) for whom the new Activities are to be created.
- Priority
- Specify here the Priority that is to be used in the new Activities. This will be shown in the field in the header of each new Activity, and will be visible in the Task Manager.
Batch Quality Settings in Standard ERP:
---
Go back to:
|