Item Effectivity
You can use this setting together with the
Item Effectivity report to monitor the use and performance of consumable Items in the production process.
You can enter separate records in this setting for each individual consumable Item to record how many Output Items it was used to produce. For example, each time you change a cutting disc in a Machine, you can enter the number of Output Items produced by the previous one in the existing Item Effectivity record, approve it, and then create a new Item Effectivity record for the new cutting disc. Alternatively, you can maintain a single record for the cutting disc as a general Item, updating the same Item Effectivity record each time you fit a new cutting disc to the Machine. This second method may help you compare cutting discs with different specifications, purchased from different Suppliers.
If you are using the first method, you can produce the Item Effectivity report using the Overview option to display the information in those records as if you were using the second method. This option adds the figures in all records with the same Item/Supplier/Machine combination to provide totals.
To work with this setting, first ensure you are in the Production module, and then click the [Settings] button in the Master Control panel or use the Ctrl-S/⌘-S keyboard shortcut to open the 'Settings' list. Double-click 'Item Effectivity' in the list. The 'Item Effectivity: Browse' window lists the Item Effectivity records that have already been entered: double-click one to modify it or click [New] to create a new record. When the record is complete, click the [Save] button in the Button Bar to save changes and close it using the close box, or click the close box if you don't want to save changes.
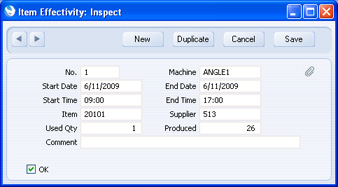
- No.
- This field contains the unique identifying number of each Item Effectivity record. This number is generated automatically.
- Machine
- Paste Special
Asset register, Assets module
- Enter the Machine to which the consumable Item has been fitted.
- Start Date, End Date
- Paste Special
Choose date
- Enter the dates when you started using the consumable Item and when you stopped using it. The End Date cannot be earlier than the Start Date.
- Start Time, End Time
- Paste Special
Current Time
- Enter the times when you started using the consumable Item and when you stopped using it.
- Item
- Paste Special
Item register
- Specify the consumable Item here. This must be an Item in the Item register.
- Supplier
- Paste Special
Suppliers in Contact register
- Specify the Supplier from whom you purchased the consumable Item.
- If you are maintaining a single Item Effectivity record for each general consumable Item, updating it each time you fit a new one, you can use this field to compare the performance of similar Items from different Suppliers.
- Used Qty
- Enter the quantity of the consumable Item that you have used. If you are maintaining a single Item Effectivity record for each general consumable Item, you should update this field each time you fit a new one to the Machine. If you are entering separate records in this setting for each individual consumable Item, you will always enter "1" here.
- You do not have to enter a Used Qty before saving an Item Effectivity record, but you must do so before marking it as OK.
- Produced
- Use this field to record the number of Output Items produced by the consumable Item. If you are maintaining a single Item Effectivity record for each general consumable Item, you should update this field each time you fit a new one to the Machine. If you are entering separate records in this setting for each individual consumable Item, enter the quantity produced when using an individual Item.
- You do not have to enter a figure here before saving an Item Effectivity record, but you must do so before marking it as OK.
- Comment
- Use this field to record any general comments about the Item Effectivity record.
- OK
- When the Item Effectivity record is complete, mark it as OK and save it. You will no longer be able to make any changes. You cannot reverse this action. If you are maintaining a single Item Effectivity record for each general consumable Item, you will need to update the record each time you fit a new one to the Machine and therefore you should never mark it as OK. An Item Effectivity record does not have to be marked as OK for it to appear in the Item Effectivity report.
---
See also:
Settings in the Production module:
See also:
Go back to: