Introduction to the Recipe Register
A Recipe is the list of the components (including quantities) needed to build an assembled Item. The Recipe is therefore the Bill of Materials for that Item.
Before you can enter a Recipe, you should enter the result of the Recipe (the assembled Item) in the Item register as described here. After defining the Recipe using the Recipe register, return to the Item record for the assembled Item and specify the Recipe on the 'Recipe' card.
If you specify that the assembled Item is a Structured Item using the options on the 'Pricing' card of the Item record, the Recipe will be applied at the moment of delivery. Enter the Item Number of the assembled Item in an Order and create a Delivery as usual. Stock levels for each of the components will be reduced according to the Recipe when you approve the Delivery. The Structured Item itself will never be held in stock.
If the assembled Item is a Stocked Item, you must build it prior to delivery using the Production register and hold it in stock. When you mark the Production record as Finished and save it, stock levels for the components will be decreased as appropriate and those for the assembled Item increased.
To work with Recipes, ensure you are in the Production module and click the [Recipes] button in the Master Control panel to open the Recipe register. Alternatively, if you are in the Stock module, click the [Settings] button in the Master Control panel and double-click 'Recipes' in the subsequent list. In both cases, click the [New] button in the Button Bar to create a new Recipe record.
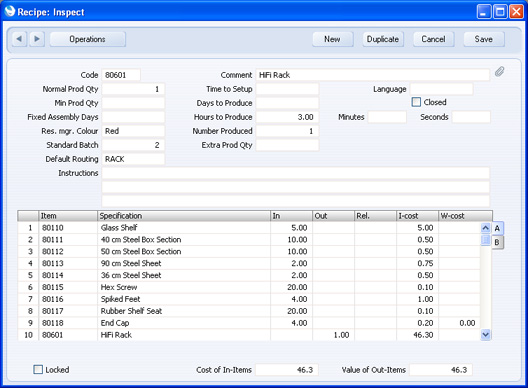
- Code
- The Code for the Recipe can be up to 20 characters long. It is recommended that you use a Code that is similar to the Item Number of the assembled Item.
- Comment
- A description of the assembly.
- Normal Prod Qty
- This field is only used if the result of the Recipe is a Stocked Item. If this is the case, specify here how many times the Recipe will usually be used in a single Production or Production Order record.
-
- If you create a Production or Production Order from a Sales Order with a Planned Delivery Date using the 'Create Planned Records' or 'Create Planned Records from Orders' Maintenance function, this figure will be placed in the Qty field in the header of the new Production or Production Order as a default if it is larger than the quantity in the Sales Order and if you are using the Always create Normal Production Qty from Planned option in the Production Settings setting.
- The Qty field in the header of a Production or Production Order is the number of applications of the Recipe. For example, if the Out quantity of the Recipe is "2" (entered in the row containing the Output Item) and the Recipe is applied five times in a Production record (i.e. the Qty in the Production header is "5"), the result will be ten units of the Output Item being added to stock.
- Take care with the Normal Prod Qty if the Output Item or any of the components are Serial Numbered at unit level. For example, a Recipe contains a Serial Numbered component with an In Qty of two and the Normal Prod Qty is also two. When you use the Recipe in a Production, the Production will contain four rows each with a In Qty of one, allowing you to enter Serial Numbers individually (In Qty * Normal Prod Qty). Therefore, you must specify a Normal Prod Qty if any of the Items are Serial Numbered. If you do not, the Serial Numbered Item will not be copied to the Production because you are effectively multplying by zero. In addition, if you are not using the Production Lines hold Actual Qty option in the Production Settings setting, you must enter "1" here. If the Normal Prod Qty should in reality be greater than one, make the adjustment by increasing the In and Out Quantities of each Item.
- Language
- Paste Special
Languages setting, System module
- Used as default in Production Orders and Productions
- The Language specified here will be copied to all Production Orders and Productions that use the Recipe, where it will determine the Form that will be used when you print documents from those records, and the printer that will be used to print them. Please refer here for more details.
- Min Prod Qty
- If you create a Production or Production Order from a Sales Order with a Planned Delivery Date using the 'Create Planned Records' or 'Create Planned Records from Orders' Maintenance function, this figure will be placed in the Qty field in the header of the new Production or Production Order as a default if it is larger than the quantity in the Sales Order. However, if you are using the Always create Normal Production Qty from Planned option in the Production Settings setting and the Normal Prod Qty immediately above is larger than this minimum, the Normal Prod Qty will be used instead.
- Time to Setup, Fixed Assembly Days, Days to Produce, Hours to Produce, Minutes, Seconds
- These fields are only used if the result of the Recipe is a Stocked Item, as follows:
- Days to Produce
- The number of days required to build a single application of the Recipe (i.e. the number of days required to build the Out Qty). One day is 24 hours.
- Hours to Produce
- The number of hours required to build a single application of the Recipe.
- Minutes
- The number of hours required to build a single application of the Recipe.
- Seconds
- The number of hours required to build a single application of the Recipe.
- If you specify any combination of Days, Hours, Minutes and Seconds, they will be added together.
- Fixed Assembly Days
- This is a constant figure irrespective of the quantity being built (i.e. it is for work that is carried out once per production run, and so will be the same irrespective of the number of applications of the Recipe). Again, one day is 24 hours.
- Time to Setup
- This is a constant figure irrespective of the quantity being built (i.e. it is for work that is carried out once per production run, and so will be the same irrespective of the number of applications of the Recipe).
- This field uses a time format. For example, if the Time to Setup is two hours, enter "02:00:00". The maximum time is 23:59:59.
- For example, the Recipe might represent the assembly of an Item from moulded plastic components. The time taken to retrieve the set of moulds from the store, order the raw materials and set up the assembly line is the same irrespective of the quantity being built. Enter this time is entered to the Fixed Assembly Days or the Time to Setup fields, depending on its duration and on whether you need to account for the costs. The remainder of the production time is taken up by pouring the plastic into the moulds, letting it cool, assembling the components and packaging them. If there is only one set of moulds, this can only be done for one unit at a time and therefore you should record this time in the Days, Hours, Minutes or Seconds to Produce fields, again depending on the duration.
- These fields will be used together with the number of Buffer Days specified in the Production Settings setting to schedule the building of assembled Items as required. With the exception of the Fixed Assembly Days field, they can also be used to calculate Work Costs. These two features are now described.
- The scheduling feature begins with the 'Create Planned Records' Maintenance function in the Sales Orders and Production modules, and with the 'Create Planned Records from Orders' function, also in the Sales Orders module. These functions create Production Orders or Productions for Stocked Items with Recipes that have been included in Sales Orders with future Planned Delivery Dates (i.e. for Items that you have sold and that you need to build or assemble). The dates of these Production Orders or Productions will be calculated using the Planned Delivery Dates of the Sales Orders, these lead times in the appropriate Recipe, the number of Buffer Days specified in the Production Settings setting, and the working hours of the Machine recorded in the Machine Hours register. This ensures you will build or assemble the goods just before they are scheduled for delivery to the Customer.
- For example:
Planned Delivery Date of Sales Order (qty 2) | January 25 | Days to Produce for the first unit (from Recipe) | 2 | Days to Produce for the second unit (from Recipe) | 2 | Fixed Assembly Days (from Recipe) | 1 | Buffer Days (from Production Settings) | 5 | | | Date of Production or Production Order | January 15 |
If the total lead time calculated in this way is not be a whole number of days, it will usually be rounded down, unless you are using the Round odd Hours to One Day option in the Production Settings setting. For example, if the lead time is 4 days 23 hours and you are not using this option, then the date of the Production or Production Order will be four days before it is needed. If you are using this option, the date will be five days before it is needed. The lead time may not be a whole number of days if you have specified a number of Hours, Minutes or Seconds to Produce (depending on the quantity to be produced), and will not be a whole number of days if you have specified a Time to Setup.
- Please refer here for details about how the Machine’s working hours (recorded in the Machine Hours register) will affect the calculation of the lead time.
- If you have specified a Number Produced in the Recipe (below), the Days, Hours, Minutes and Seconds to Produce will be divided by this figure before being included in the calculation.
- These times will also be used when calculating Start Dates in Production Plans in the MRP module.
- The 'Create Planned Records' functions will also create any necessary Purchase Orders for the components. These will be dated using the Delivery Days from the Default Purchase Item for the components, ensuring they arrive in time for the assembly process to be completed.
- The costing feature begins with the Add Work Cost option in the Production Settings setting. If you are using this option, a Work Cost will be added to each new Recipe automatically. This Work Cost will be calculated using the Work Cost per Hour specified in the same setting and the time required for the Recipe (the total of the Time to Setup and the Days, Hours, Minutes and Seconds to Produce: the Fixed Assembly Days is not included). The Work Cost will be placed in the W-cost field in the last Input row in the Recipe.
- For example:
Days to Produce (1 day, converted to hours) | 24 | Hours to Produce | 3 | Time to Setup (Hours) | 3 | Total Hours | 30 | | | Work Cost per Hour | 0.10 | | | Total Work Cost (for one application of the Recipe, placed in the W-cost field in the last Input row) | 3.00 |
The calculation of this Work Cost figure is also affected by the Number Produced. Please refer to the description of this field below for details.
- You cannot change this calculated Work Cost figure, but you can in effect adjust it by specifying another Work Cost (which can be negative if necessary) in one of the other Input rows.
- This feature does not apply to Recipes with Routings.
- Closed
- Check this box if the Recipe can no longer be used. Closed Recipes will appear in the 'Recipes: Browse' window but not in the Recipes 'Paste Special' list.
- If the result of a Closed Recipe is a Structured Item and you use that Item in an Order, Invoice or other sales or stock transaction, you will not be able to save the transaction. It is therefore recommended that you mark the Structured Item as Closed as well, to remove it from the Item 'Paste Special' list so that you do not use it by mistake in sales transactions.
- Res. mgr. Colour
- Paste Special
Choices of possible entries
- All Accepted and Started Production Orders with a particular Recipe will appear in the same colour in the Resource Planner. Choose that colour using this field.
- Number Produced
- The Time to Setup, the Days, Hours, Minutes and Seconds to Produce and the Fixed Assembly Days fields above usually refer to one application of the Recipe i.e. they are the times required to produce the Out Qty of the Output Item. If this is not the case, specify here the number of applications of the Recipe that these times refer to.
- First, the Number Produced will affect the calculation of lead times when you use the 'Create Planned Records' and 'Create Planned Records from Orders' functions to create Productions or Production Orders, and also when you create Productions or Production Orders from the MRP module. If you have specified a Number Produced, the Days, Hours, Minutes and Seconds to Produce will be divided by this figure before being included in the calculation. To repeat the example previously used in the section describing the various time fields above but with a Number Produced of two:
Planned Delivery Date of Sales Order (qty 2) | January 25 | Days to Produce for the first unit (from Recipe, divided by 2) | 1 | Days to Produce for the second unit (from Recipe, divided by 2) | 1 | Fixed Assembly Days (from Recipe) | 1 | | | Date of Production or Production Order | January 17 |
Second, if you are using the Add Work Cost option in the Production Settings setting to have a Work Cost added to each new Recipe automatically, entering a Number Produced will change the calculation of the Work Cost. Again, repeating the example used in the description of the various time fields above, the effect will be as follows:Days to Produce (1 day, converted to hours) | 24 | Hours to Produce | 3 | Time to Setup (Hours) | 3 | Total Hours | 30 | | | Work Cost per Hour | 0.10 | | | Total Work Cost (for one application of the Recipe) | 3.00 | | | Number Produced | 2 | | | Work Cost per Unit (placed in W-cost field in last Input row) | 1.50 |
This field is also used together with the Production Time Entry interface and the Add Work Cost option. The Add Work Cost option means that Setup and Run Time Activities will both be created for each Production that you work on, and a Work Cost will be added to each Production automatically. This will be calculated using the total Cost (Time) of the Setup and Run Time Activities and the Work Cost per Hour (also specified in the Production Settings setting). If you have specified a Number Produced in the Recipe, the Cost (Time) of the Setup Activity will be divided by this figure before being added into the calculation.
- Standard Batch
- Specify here the number of applications of the Recipe that the Machine will usually build. For example, if you need to fill the Machine with enough raw materials to produce four applications of the Recipe each time you use it, enter "4" in this field. When you create a Production from a Production Order using the 'Finish Batch' function on the Operations menu, this figure will be copied to the Qty field in the header of that Production (irrespective of the Qty in the Production Order).
- Take care with the Standard Batch if the Output Item or any of the components are Serial Numbered at unit level. For example, a Recipe contains a Serial Numbered component with an In Qty of two and the Standard Batch is also two. When you create a Production from a Production Order that uses the Recipe, the Production will contain four rows each with a In Qty of one, allowing you to enter Serial Numbers individually (In Qty * Standard Batch). Therefore, you must specify a Standard Batch if any of the Items are Serial Numbered. If you do not, the Serial Numbered Item will not be copied to the Production because you are effectively multplying by zero. In addition, if you are not using the Production Lines hold Actual Qty option in the Production Settings setting, you must enter "1" here. If the Standard Batch should in reality be greater than one, make the adjustment by increasing the In and Out Quantities of each Item.
- Default Routing
- Paste Special
Routings setting, Production module
- If the Recipe represents a Production process that has been divided into stages, specify a Routing here. This is effectively a schedule of the process, specifying the stages and the order in which they should be carried out.
- If the Recipe has a Routing, you should assign a Material to each of the Input and Output Items (on flip B). Materials will connect the Items to the relevant stages in the process.
- You cannot enter a Work Cost in any of the Input rows if the Recipe has a Routing. Instead, you should record the Work Costs either by specifying times in each Standard Operation or using Activities. Please refer to the description of the Time options (Actual and Fixed) in the Productions Settings setting for more details.
- Note that if you use a Recipe with a Routing in a Production Order, you cannot then work on the resulting Productions using the Production Time Entry interface.
- Instructions
- Use these three lines to record instructions about how the Recipe should be used. These instructions will be copied to Production Orders.
---
In this chapter:
Go back to:
|