Replaced Items
This page describes the Replaced Items setting in the Service Orders module.
---
The Replaced Items setting keeps a record of the occasions both when the repair of an Item proved not to be possible and it was exchanged for a new one and of the occasions when you needed to send an Item back to its manufacturer for repair or exchange.
When you sign such an Item into your workshops, follow these steps when it becomes apparent that repair is not possible (or is uneconomic):
- If you need to send the Item back to its Supplier for exchange or credit, enter a record in the Service Stock Transaction register. Add a row for the Item to the 'Items' card with an Out Quantity of one and the Supplier specified on flip D.
If there is no need in reality to send the Item back to a Supplier (perhaps because it is clearly no longer operational and its warranty has expired), it may be appropriate to create a dummy Supplier record in the Contact register for this purpose. You must specify a Supplier on flip D to be able to follow this sequence.
- When you mark the Service Stock Transaction as OK and save, the Item will be signed out of your workshop and a record will be created in the Replaced Items setting, as shown below:
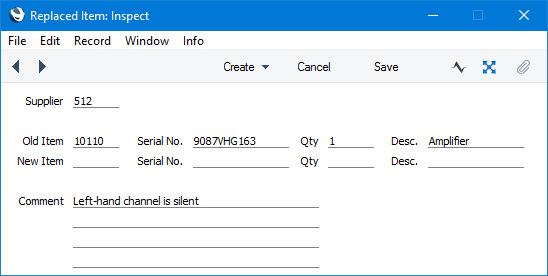
It is not possible to enter records directly to the Replaced Items setting. You can only add records to this setting remotely by marking records in the Service Stock Transaction register with Out Quantities and Suppliers as OK and saving.
- If you sent the Item back to the Supplier for repair, on its return to your company enter a new Service Stock Transaction signing it back into the workshop. You should then open the record in the Replaced Items setting from the previous step and copy the Item Number and Serial Number from the fields on the first row to those on the second. You can enter an appropriate comment if necessary. Finally, you should enter a second new Service Stock Transaction to sign the Item out of your workshop when you return it to the Customer.
- If you sent the Item to the Supplier for exchange, on the arrival in your workshop of its replacement you should first add a new row to the parent Service Order with the new Serial Number. Then, enter a new Service Stock Transaction signing it into the workshop and carrying a record of its Serial Number. You should copy this Serial Number to the new Serial No. field (on the second row) of the record in the Replaced Items setting from step 2. You can enter an appropriate comment if necessary. Finally, you should enter a second new Service Stock Transaction to sign the Item out of your workshop when you hand it over to the Customer.
- If you discarded the Item and replaced it with a new unit from your stock, review the Replaced Item record from step 2 and enter the Item Number of the new Item in the New-Item field, using 'Paste Special' if necessary. Move to the New Serial No. field: 'Paste Special' here will give a list of Serial Numbers for the Item that you currently have in stock (i.e. in stock for resale, not in the workshop). Select one, enter a Quantity of one in the next field and save the record. Note that the Replaced Items setting is purely archival: it has no effect on stock levels. You will therefore need to issue a Delivery from a Sales Order, raise an Invoice or create a Stock Depreciation record (depending on your normal practice) for the Item/Serial Number that your company is supplying so that stock levels are amended accordingly.
---
Go back to: