Introduction to the Recipe Register
Assembled Items are Items that are constructed by your company from other Items (i.e. from components). Two different kinds of assembled Items are available, depending on whether the Production module is installed:
- Structured Items
- If the Production module is not installed, an assembled Item must be entered as a Structured Item (using the options on the 'Pricing' card of the Item screen) and stock levels will not be maintained. It is assumed that the Structured Item is assembled at the moment the Delivery is made. At that moment, stock levels of the components will be reduced.
- Stocked Items
- The Production module creates "Productions". These are normally the result of a production order. When a Production is marked as "finished", the stock levels of the input Items are reduced, and the stock of the output Item is increased. To ensure this happens, any such output Item should be entered as a Stocked Item. Such Items can only be built using the Production module, and are built and held in stock in advance of delivery.
- An input Item in a Recipe can be a sub-assembly. If so, it should be a Stocked Item which itself is built in the Production register in the Production module, so that stock levels rise and fall as units are built and then used as sub-assemblies. So, to use sub-assemblies, the Production module must be installed.
In both situations, the assembly process (the quantity required of each component and the resulting stock movements) is governed by Recipes. Below, the concept is explained using an example
Structured Item.
Assume that you are assembling a stereo system from a number of components such as an amplifier, loudspeakers etc., and that the system is sold as a separate single Item. Begin by entering "Stereo System" to the Item register, and click the Structured Item button on the 'Pricing' card.
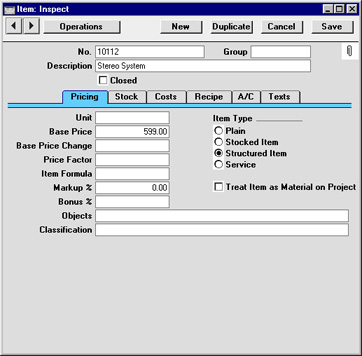
On the
'Recipe' card of the Item record you indicate a Recipe for the Item. We will define a Recipe below. When an Order is recorded in the Sales Orders module, you will use the Item Code for Stereo System. When the Order is delivered, the stock levels of each of the components will be reduced according to the Recipe, i.e. for the amplifier, loudspeakers etc. The stock balance of the System is thus dependent on the availability of the components.
In defining the Recipe for the Stereo System, ensure you use the same Recipe Code that you entered on the 'Recipe' card of the Item record. In the Stock module, select 'Recipes' from the Registers menu or click the [Recipes] button in the Master Control panel. Then click the [New] button in the Button Bar to create a new Recipe record.
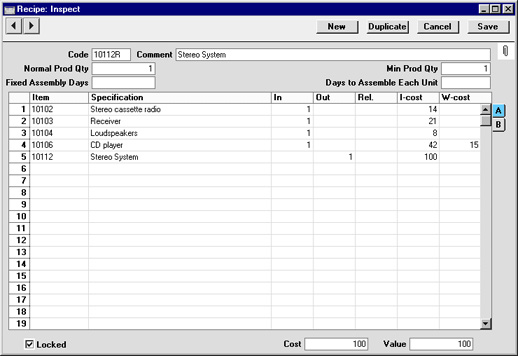
- Code
- The Code for the Recipe can be up to 20 characters long. It is recommended that the Code used is similar to the Item Code of the assembled Item.
- Comment
- A description of the assembly.
- Normal Prod Qty
- This field can only be used if the Production module is installed (i.e. when the result of the Recipe is a Stocked Item). Please click here for a description.
- Min Prod Qty, Fixed Assembly Days, Days to Assemble Each Unit
- Similarly, these fields can only be used if the Production module is installed.
Use the grid area that takes up most of the screen to list the input Items (i.e. the components that will be used to build the final assembly). On the last row of the grid, enter the Item Number of the assembly or the finished product (i.e. the result of the Recipe). If the Production module is not present, the result of the Recipe must be a
Structured Item. If the Production module will be used to build the Item, it should be a
Stocked Item.
Flip A
- Item
- Paste Special
Item register
- Enter the Item Number of each component Item. On the final row, enter the Item Number of the finished product.
- Specification
- Hansa fills in the Item name.
- In
- Enter the quantity of each component required to make or build the finished product. Do not enter any inputs for the assembly on the last line.
- Out
- This field contains the quantity of assembled Items that can be made from the components listed above. Usually, this will be just one, and it must be one if the Recipe relates to an Item.
- I-cost
- Input cost value. If the row contains an input Item, enter the Cost Price for one unit of the Item. A default value will be brought in from the Item record. The cost shown in this field is NOT the same as the FIFO stock value.
- If the row contains an output Item (i.e. the assembled Item), enter the cost value of that Item. This will usually be the sum of the Cost Prices of the input Items, taking quantities into account.
- The input costs are totalled by Hansa and are shown in the Cost field below.
- W-cost
- Work cost value. Enter a work cost for inputs and/or outputs. Usually, this will be cost of the labour required to build the assembled Item. Work cost values are added to the Cost and shown in the Value field below.
Flip B
- Description
- Any notes about the Item can be recorded here.
- Recipe
- This field shows whether the Item is an assembly (i.e. it is one with a Recipe specified on its 'Recipe' card. This is updated automatically by Hansa and can't be changed.
Footer
- Locked
- Once you are certain the Recipe is correct, you should check this box to prevent further changes. Once a Recipe has been used in a transaction (e.g. Delivery or Production), it should not be changed because doing so may introduce inaccuracies into the stock records.
- If it subsequently becomes necessary to change a Recipe, you should not do so. Instead you should create a new one (and attach it to a new Stocked or Structured Item).
! | Do not change a Recipe once it has been used in a stock transaction. |
|
- Cost
- This field contains the sum of the input costs.
- Value
- This field contains the sum of the input costs and the work costs. This value must be transferred manually to the Cost Price field on the 'Costs' card of the Item record for the Structured Item.