Entering a Production Record - Items Card
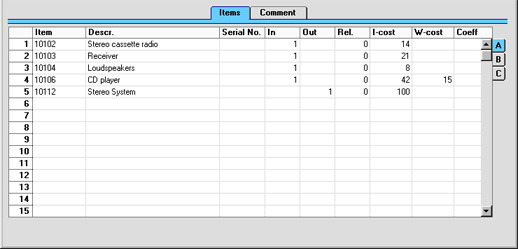
When a Recipe is specified, the appropriate input and output Items together with quantities and Cost Prices are listed in the grid. Any modifications made will apply to this Production record only. If no Recipe has been entered, the grid can be used to build up an ad hoc recipe to be used for this Production record only.
Flip A
- Item
- Paste Special
Item register
- Default taken from Recipe
- The input Items (i.e. the components) are listed first. Enter the Item Number of each of the components which make up the assembled Item.
- If a component is itself an assembly, sufficient stock should first be built up using other Production records. Each Production record is responsible for a single level of assembly: it will not create sub-assemblies as well.
- On the last row(s) enter the Item Number of the assembly or the finished product, i.e. the result of the Production. This must be a Stocked Item. More than one Stocked Item can result from a single Production record.
- Descr.
- Item description from the Recipe or Item record.
- Serial No.
- Paste Special
Serial Numbers of Items in stock
- In the case of input Items, if necessary enter the Serial Number of the Item being used in the assembly process. In the case of output Items, enter the Serial Number given to the assembly.
- Items which are serial numbered at unit level must be recorded on separate rows of the Production each with a Quantity of one. This enables the recording of separate Serial Numbers and their correct removal from stock.
- If a large quantity of a Serial Numbered Item is assembled in a single Production record, the 'Generate Serial Nos for Out Items' function on the Operations menu can aid the entry of consecutive Serial Numbers. Enter the appropriate number of rows with output Items and specify the lowest Serial Number for the first one. Then select the function: the remaining rows will gain a Serial Number, each incremented by one.
- If no Location is specified, the 'Paste Special' list will show the Serial Numbers of Items in all Locations, with an indication of the Location in which each Item is stored. However, if you have specified a Location, only those Serial Numbers stored in that Location will be shown.
- The No Serial No. On Goods Receipts option in the Stock Settings setting in the Stock module must be switched off if you are using the Production register. You must enter Serial Numbers for components and the assembly if so determined by the appropriate Item record.
- In
- Default taken from
Recipe
- Enter the quantity of each component required to make or build the finished product. Do not enter any inputs for the assembly on the last line.
- If a Nominal Ledger Transaction is generated from this Production record, its credit amount will be taken from the total I-Cost of rows with an In quantity (i.e. input Items).
- Out
- Default taken from
Recipe
- This field contains the quantity of assembled Items that can be made from the components listed above. Usually, this will be just one, and it must be one if the Production relates to an Item.
- If a Nominal Ledger Transaction is generated from this Production record, its debit amount will be taken from the total I-Cost of rows with an Out quantity (i.e. output Items).
- Rel.
- Default taken from
Recipe
- Relativity. This field is only used if the Production process causes more than one Item to be assembled (i.e. with different Item Numbers). In each row representing an output Item, enter a percentage figure. When calculating the input cost of each assembly (using the 'Calculate FIFO' function on the Operations menu), the total cost of the components will be distributed according to the percentages entered here.
- I-cost
- Default taken from
Recipe
- Input cost value (per unit). If the row contains an input Item, enter the unit Cost Price of the Item. A default value will be brought in from the Recipe: this is therefore a fixed figure and NOT the same as the FIFO stock value. To show the FIFO stock value, use the 'Calculate FIFO' item on the Operations menu. If, in the Stock Settings setting in the Stock module, you have chosen to use the FIFO Calculated Automatically option, FIFO stock values will be placed here when the Production record in marked as Finished and saved.
- Since a Nominal Ledger Transaction may result from this action which will affect your stock valuation in the Nominal Ledger, care should be taken to ensure that the correct Input cost values are shown. The FIFO Calculated Automatically option should be used if the Nominal Ledger stock valuation is based on FIFO values, but it should be turned off if it is based on fixed costs.
- If the row contains an output Item (i.e. the assembled Item), enter the cost value of that Item. This will usually be the sum of the Cost Prices of the input Items, taking quantities into account. The 'Calculate FIFO' function and automatic FIFO calculation feature will both place the total of the FIFO values of the components here. If there is more than one output Item, this total will be distributed according to the percentages entered in the Rel. column.
- W-cost
- Default taken from
Recipe
- Work cost value (per unit, determined by the Quantity in the header). Enter a work cost for inputs and/or outputs. Usually, this will be cost of the labour required to build the assembled Item.
- The Work Cost should be entered to one of the rows featuring an input Item, as shown in the sample illustration above. This ensures the work cost will correctly be included in the credit amount in the Nominal Ledger Transaction generated from this Production record.
- Coeff
- Default taken from
Item
- The Unit Coefficient of the Item is shown here, taken from the 'Stock' card of the Item. If you are maintaining stock quantities using different units of measurement, this coefficient is the ratio between those units of measurement.
Flip B
- Objects
- Paste Special
Object, System module
- Default taken from Item
- Up to 20 Objects, separated by commas, can be assigned to this row. They will be transferred to the Nominal Ledger Transaction generated when this Production is marked as Finished, providing a flexible method of analysis that can be used in Nominal Ledger reports. You might define separate Objects to represent different departments, cost centres or product types.
- In the Nominal Ledger Transaction generated from this Production record, any Objects specified here will be assigned to the credit posting for this Item. This assignment will merge these Objects with those of the parent Production record (shown on the 'Comment' card).
Flip C
- Width, Height, Depth
- Default taken from
Item
- These fields contain the dimensions of the Item.
- If the Item is one that is built by area or volume, you can have the Input or Output Quantity calculated by multiplying the dimensions together. If you would like to use this feature, first check the Enable Quantity Calculation box in the Item Settings setting in the Sales Ledger. Then, check the Calculate Quantity box for the Unit that has been assigned to the Item. If the Item is built by area, choose the Two Dimensions option in the Unit record, and the Input or Output Quantity will be calculated from the Width and Height. If the Item is built by volume, choose the Three Dimensions option in the Unit record, and the Input or Output Quantity will be calculated from the Width, Height and Depth. Please refer to the description of the Units setting for details and an example.
|