Additional Production Costs with Production Operations
When you use Production Operations to build a Production, you can record four separate types of running costs, as follows:
- Labour
- the cost of labour
- Setup
- the cost of setting up the Machine e.g. calibration or replenishing fluids or consumables
- Move
- the cost of moving parts either from stock to the first Production Operation or from one Production Operation to the next
- Queue
- the cost incurred in waiting for parts to be ready e.g. waiting for paint to dry or heated parts to cool. Queue time is also known as "non-instant availability".
You can calculate these four running costs using one of two methods:
- Actual Time
- The costs will be based on the time actually taken to complete a Production Operation
- Fixed Time
- Costs will be fixed in advance of the Production Operation taking place.
The Running Cost per Hour in the Asset record is also used to calculate a Machine's running costs if you are using Production Operations. Therefore you should not include this cost in one of the four cost types described above if you are using this feature. However, you will need to remember to specify a Machine in each Production Operation (the Machine cannot be copied from the Production because it is likely that each Production Operation will use a different Machine). If this is impractical, then you can include each Machine's running costs in one of the four cost types instead. This will be the case in this example.
Follow these steps:
- In the Production Settings setting, use the Time options on the 'Cost Items' card to choose whether you will record Actual or Fixed Time:
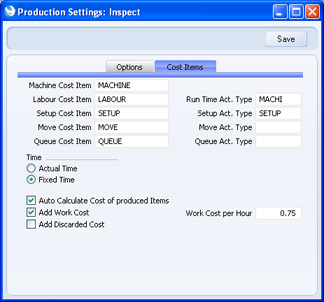
If you choose the Fixed Time option as in the illustration, you should also specify Labour, Setup, Move and Queue Cost Items. When you create each Production Operation, it will contain an extra row for each cost type, using the Items specified here. If you choose the Actual Time option, you only need specify a Labour Cost Item. In both cases, enter a Work Cost per Hour.
Steps 2-5 below describe the Fixed Time option, while steps 6-9 describe the Actual Time option.
- If you are using the Fixed Time option, you should now specify the times required to complete each Operation, on the 'Time' card of each Standard Operation record:
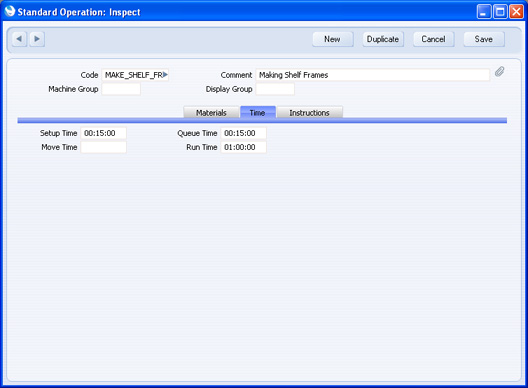
These are the times required for the whole Operation, not per unit.
- When you create the Routing record, the times from each Standard Operation will be copied to flip B. You can change the times for a particular Routing if necessary. For example, a Standard Operation might contain the times required to complete four Items, as the usual quantity produced. A particular Recipe may require five to be produced, so you will need to adjust the times in the Routing accordingly.
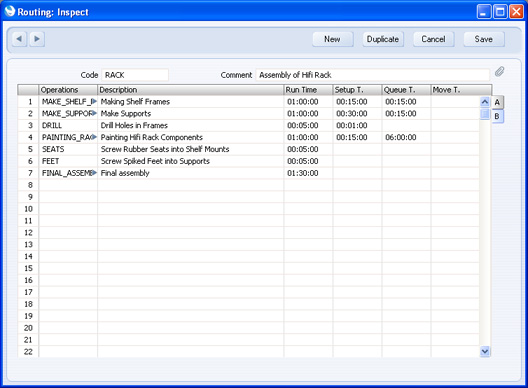
- When you create the Production Operations for a Production, the Cost Items specified in the Production Settings setting will be added to the 'Items' card of each Production Operation, with quantities calculated from the Routing:
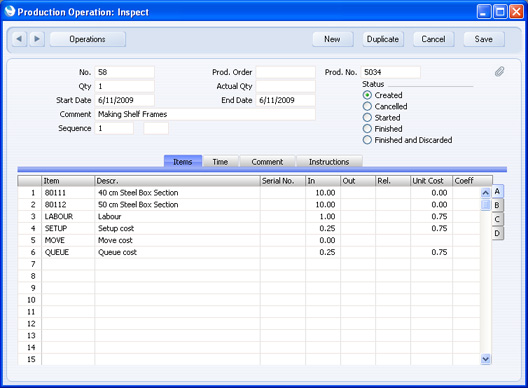
- As normal, when work starts, mark the Production Operation as Started and save it. When work finishes, enter the quantity produced in the Actual Qty field, mark the Production Operation as Finished and save it. The relevant quantities of the Input Items will be removed from stock. If you are updating the stock valuation in the Nominal Ledger from each Production Operation, the total value of the four cost items will be credited to the Work Cost Account and debited to the Work in Progress Account (together with the value of the Input Items removed from stock). The value will be calculated using the Work Cost per Hour specified in the Production Settings setting.
In this case, the various calculations are:
Set Up Cost (15 minutes @ 0.75 per hour from Production Settings) | 0.1875 |
Labour (1 hour @ 0.75 per hour from Production Settings) | 0.75 |
Queue Cost (15 minutes @ 0.75 per hour from Production Settings) | 0.1875 |
Total (rounded to two decimal places) | 1.13 |
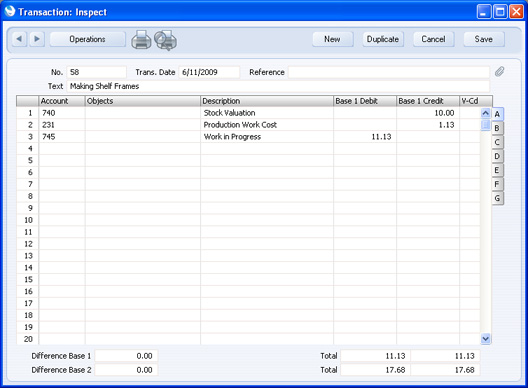
- If you are using the Actual Time option in the Production Settings setting, you need to use Activities to record the time you spend on each Production Operation. You should create these Activities from each Production Operation while its Status is Created or Started, using the 'Create Activity' function on the Operations menu. Before selecting this function, enter Start and End Dates and Times in the Production Operation, as these will be transferred to the Activity:
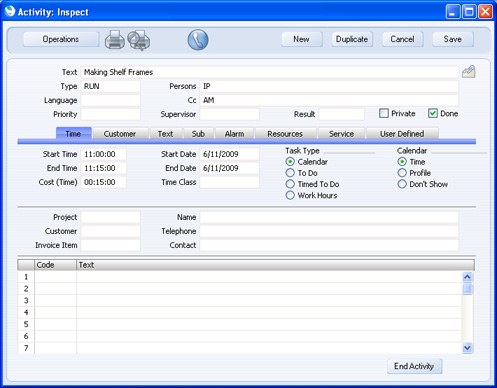
The Activity Type will be taken from the Activity Types, Subsystems setting in the CRM module. If you entered your Signature on the 'Comment' card of the Production Operation, it will be copied to the Persons field in the Activity. Otherwise, enter it to the Activity yourself. Mark the Activity as Done and save.
If you create these Activities in advance, you can also use them for scheduling purposes, as described on the Scheduling Production Operations page.
- Repeat step 6 as necessary.
- Choose 'Add Labour' from the Operations menu of the Production Operation. This will add a row to the Production Operation with the Labour Cost Item and Work Cost per Hour specified in the Production Settings setting. The quantity will be the total time for all Done Activities created from the Production Operation:
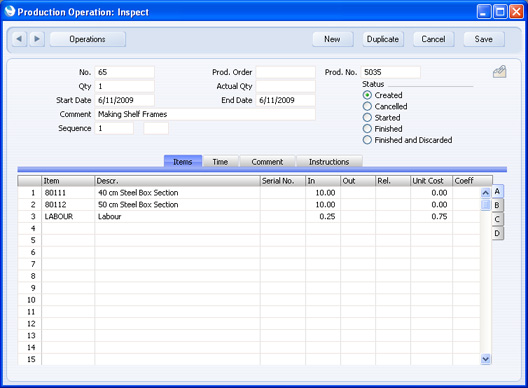
- When work finishes, enter the quantity produced in the Actual Qty field, mark the Production Operation as Finished and save it. The relevant quantities of the Input Items will be removed from stock. If you are updating the stock valuation in the Nominal Ledger from each Production Operation, the value of the Labour Cost Item will be credited to the Work Cost Account and debited to the Work in Progress Account (together with the value of the Input Items removed from stock).
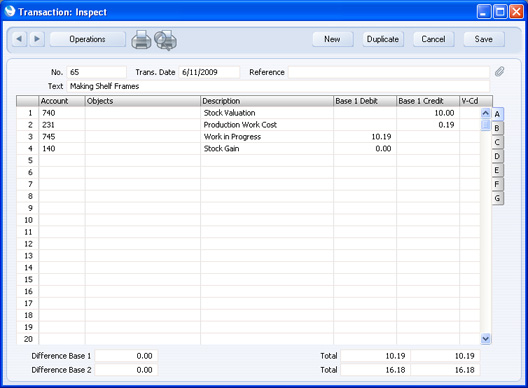
- If you are using the Fixed Time option as described in steps 2-5, you can also use the Actual Time method ('Create Activity' and 'Add Labour') to add an extra cost to a particular Production Operation.
---
In this chapter:
See also:
Go back to: