Materials, Standard Operations, Routings - The Routings setting
Having used
Standard Operations to divide a Production process into stages, and
Materials to assign the Input and Output Items to those stages, you can now use Routings to determine the order in which the Operations are to be carried out.
To work with the Routings setting, first ensure you are in the Production module, and then click the [Settings] button in the Master Control panel or use the Ctrl-S/⌘-S keyboard shortcut to open the 'Settings' list. Double-click 'Routings' in the list. The 'Routings: Browse' window lists the Routing records that have already been entered: double-click one to modify it or click [New] to create a new record. When the record is complete, click the [Save] button in the Button Bar to save changes and close it using the close box, or click the close box if you don't want to save changes.
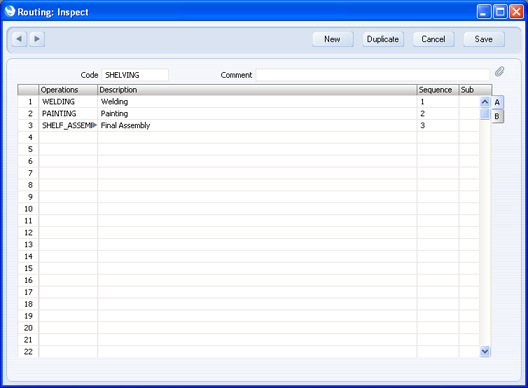
Header
- Code
- Specify a unique identification Code for the Routing record.
- Comment
- Enter a name for the Routing record.
A Routing record is a list of the Operations that make up a Production process. In effect, it's a schedule of the process. Use the grid that takes up the majority of the window to list those Operations, and to specify the order in which they are to be carried out.
Flip A
- Operations
- Paste Special
Standard Operations setting, Production module
- When you enter a Standard Operation here, its Comment and the various times will be brought in to the appropriate fields.
- Description
- When you choose a Standard Operation in the field above, its Comment will be placed here.
- Sequence, Sub
- Use the Sequence field to specify the order in which the Standard Operations are to be carried out.
- If more than one Operation can be carried out at the same time, give them the same Sequence numbers, and different Sub Sequence numbers. For example, it might be possible to build two sub-assemblies simultaneously, because the building of one does not depend on the other one already existing. But both sub-assemblies must be complete before they can be brought together to make a whole, so the assembly stage should have a later Sequence number.
Flip B
- Setup Time, Queue Time, Move Time, Run Time
- Default taken from
Standard Operation
- Used as default in Production Operations
- Use these four fields to stipulate the time required for the Operation, as follows:
- Setup
- the time required to set up the Machine or otherwise prepare for the Operation e.g. calibration or replenishing fluids or consumables.
- Queue
- the time required to wait for parts to be ready from the previous Operation e.g. waiting for paint to dry or heated parts to cool. Queue time is also known as "non-instant availability".
- Move
- the time required to move parts from stock or from the previous Operation.
- Run Time
- the time required for the Operation itself.
These are the times required for the entire Standard Operation, not to produce one unit. They will be copied from the Standard Operation record and from here onward to each Production Operation created using the Standard Operation as a template. You can adjust the times here if necessary (for example, the times in the Standard Operation may be sufficient to produce four units, but the particular application of the Operation in a particular Routing may produce five units).
If you are using the Fixed Time option in the Production Settings setting, the 'Items' card of each Production Operation will contain extra rows for each type of Time. The Item Numbers in these rows will be the Setup, Queue, Move and Labour Cost Items specified in the Production Settings setting, and the Unit Cost in each case will be the Work Cost per Hour in the same setting. The In Qty in each of these rows (number of hours) will be the times from the relevant Routing row which, by default, will be the times specified here. These extra rows allow you to account for the running costs of the Operation.
If you are using the Actual Time option in the Production Settings setting, you can still specify times here. In this case, these times will not be used to account for the running costs of the Operation, but you can use them as guides, to give an idea of how much time is required for the Operation (they will be copied to the 'Time' card of each Production Operation).
Once you have entered a Routing record, the division of a Production process into stages is almost complete. The final task is to enter the Routing in the Default Routing field in the Recipe:
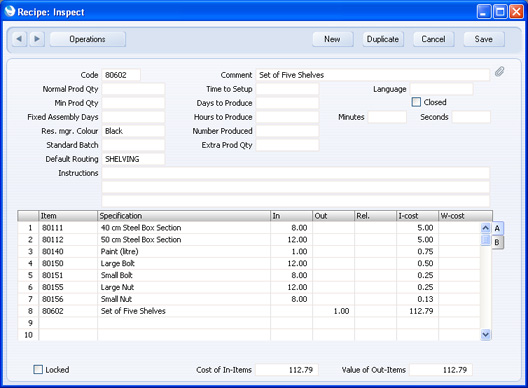
Having done so, when you specify the Recipe in a Production, the Default Routing will be copied from that Recipe to the Production as well. You can then use the
'Create Production Operations' function on the Operations menu to create the Production Operations as instructed in the Routing and as described in the sequence towards the end of the page describing the
Materials setting. The Production Operation register is described
here.
---
Settings in the Production module:
Go back to: