Materials, Standard Operations, Routings - The Standard Operations setting
This page describes the Standard Operations setting in the Production module, one of the settings that you need to configure when dividing Productions into stages. You can find more details about this configuration process on the following pages:
---
The first step when dividing a Production process into stages is to determine what the stages are. You should enter each stage as a separate record in the Standard Operations setting.
Standard Operations are essentially templates. They should contain the usual specifications for each stage in the process. When you create Production Operations from a Production, they will be created using the relevant Standard Operations as templates. Production Operations represent the same stages in the process as the Standard Operations, but are specific to the individual Production. If there is something unusual about a Production Operation (e.g. it takes longer than expected to complete), you can register this in the Production Operation without disturbing the template Standard Operation.
To work with the Standard Operations setting, first ensure you are in the Production module. Then, if you are using Windows or macOS, click the [Settings] button in the Navigation Centre or use the Ctrl-S/⌘-S keyboard shortcut to open the 'Settings' list. If you are using iOS or Android, select 'Settings' from the Tools menu (with 'wrench' icon). Double-click (Windows/macOS) or tap (iOS/Android) 'Standard Operations' in the list. The 'Standard Operations: Browse' window listing the Standard Operations records that have already been entered opens. Select 'New' from the Create menu (Windows/macOS) or from the + menu (iOS/Android) to create a new record. When the record is complete, click the [Save] button (Windows/macOS) or tap √ (iOS/Android) to save changes and close it using the close box or by tapping <. Click the close box or tap < if you don't want to save changes.
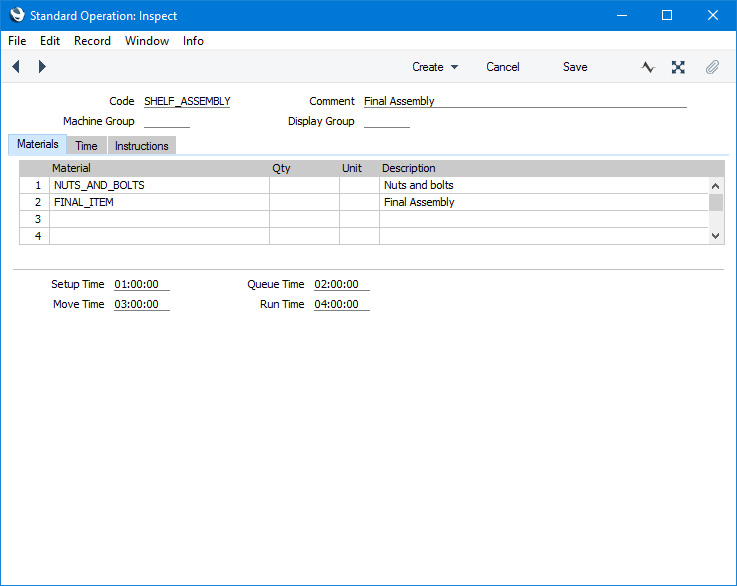
Header
- Code
- Specify a unique identification Code for the Standard Operation.
- Comment
- Enter a name for the Standard Operation.
- Machine Group
- Paste Special
Machine Groups setting, Production module
- Used as default in Routing rows and Production Operations
- Specify here the Machine Group that contains the Machines that you can use to carry out the work represented by the Standard Operation.
- The Machine Group will be copied to each Routing row in which the Standard Operation has been quoted and from there to the Production Operations that use the Standard Operation as a template.
- Display Group
- Paste Special
Display Groups setting, System module
- Used as default in Production Operations
- Specify here the Display Group that contains the Persons that can carry out the work represented by the Standard Operation.
- The Display Group will be copied to each Production Operation that you create from this template.
Materials Card
Use the 'Materials' card to list the Materials that will be used as part of the Standard Operation. When you
create a Production Operation from a Production using the Standard Operation as a template, every Input and Output Item in the Production that has been assigned one of these Materials will be copied to the Production Operation. Please refer to the description of the Materials setting
here for an example.
- Material
- Paste Special
Materials setting, Production module
- Choose a Material from the Materials setting. You can also enter an ad hoc Material if necessary.
- Qty
- When you create a Production Operation from a Production using the Standard Operation as a template, every Input and Output Item in the Production with the Material specified above will be copied to the Production Operation. Usually, the In Qty or Out Qty as appropriate will be copied from the Production row to the corresponding Production Operation row. However, if you enter a Quantity here, it will be copied to the relevant Production Operation row instead. If the Production row has an In Qty, this Quantity will be copied to the In Qty field in the Production Operation row. Otherwise, it will be copied to the Out Qty field. This figure will therefore take priority over the In and Out Quantities in the Production (which themselves will have been taken from the Recipe). As this figure applies to a Material not an Item, it will be used as the In or Out Quantity for every Item in the Production with that Material.
- Unit
- Paste Special Units setting, Sales Ledger
- Enter the Unit that the Quantity above refers to. This is for information only.
- Description
- The Description is copied from the Materials setting.
Time Card

- Setup Time, Queue Time, Move Time, Run Time
- Used as default in
Routings
- If you are using the Fixed Time option in the Production Settings setting, use these four fields to stipulate the time required for the Standard Operation, as follows:
- Setup
- the time required to set up the Machine or otherwise prepare for the Standard Operation e.g. calibration or replenishing fluids or consumables.
- Queue
- the time required to wait for parts to be ready from the previous Standard Operation e.g. waiting for paint to dry or heated parts to cool. Queue time is also known as "non-instant availability".
- Move
- the time required to move parts from stock or from the previous Standard Operation.
- Run Time
- the time required for the Standard Operation itself.
These are the times required for the entire Standard Operation, not to produce one unit. They will be copied to the Routing record and from there to each Production Operation created using the Standard Operation as a template. You can adjust the times in the Routing if necessary.
If you are using the Fixed Time option in the Production Settings setting, extra rows for each type of Time will be added to the 'Items' card of each Production Operation automatically. The Item Numbers in these rows will be the Setup, Queue, Move and Labour Cost Items specified in the Production Settings setting, and the Unit Cost in each case will be the Work Cost per Hour in the same setting. The In Qty in each of these rows (number of hours) will be the times from the relevant Routing row which, by default, will be the times specified here. These extra rows allow you to account for the running costs of the Operation.
If you are using the Actual Time option in the Production Settings setting, leave these fields empty.
Instructions Card
Use the 'Instructions' card to record details about how to carry out the Standard Operation. These Instructions will be copied to the 'Instructions' card of each Production Operation.
Dividing Productions into Stages - Configuring Materials, Standard Operations and Routings:
---
Go back to: