Production Settings - Cost Items Card
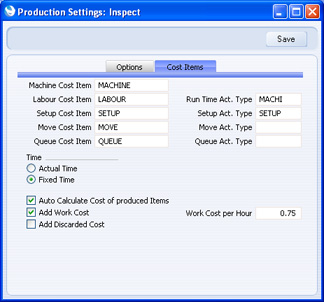
- Machine Cost Item
- Paste Special
Item register
- The Auto Calculate Cost of Produced Items option (below) allows you to record the running costs of the Machines used in Productions. If you are using this option, you must also specify a Machine Cost Item here, you should specify Running Costs/hr in the Asset records for your Machines ('Costs' card) and you should specify such an Asset in the Machine field in each Production.
- If you are using this feature, an extra row containing this Item will be added to each Production when you first save it. This row will record the running cost of the Machine used during the Production process. The running cost will be taken from the Running Costs/hr field in the relevant Asset record, and from the Start and End Time of the Production. When you mark the Production as Finished and save it, the running cost will be added to the value of the assembled Item (i.e. it will be debited to the Stock Account), and it will be credited to the Production W-cost Account.
- The choice of the Production W-cost Account will depend on whether you are using the Use Item Groups for Cost Accounts option in the Cost Accounting setting in the Stock module. If you are, and you specify a Machine Cost Item here that belongs to an Item Group in which you have specified a Production W-cost Account, that Account will be used. If you are not using this option or the Item Group does not have a Production W-cost Account, the W-cost Account will be taken from the Account Usage Stock setting.
- If a Production has a Routing, the extra row for the running cost will not be added to the Production, but instead will be added to each Production Operation. You will need to remember to specify a Machine in each Production Operation yourself before the extra row can be added, as the Machine will not be copied from the Production.
- This Item must be a Service Item.
- Labour Cost Item, Setup Cost Item, Move Cost Item, Queue Cost Item
- Paste Special
Item register
- If a Production has a Routing, running costs will be calculated at Production Operation level. You can record four separate types of running costs, as follows:
- Labour
- The cost of labour.
- Setup
- The cost of setting up the Machine e.g. calibration or replenishing fluids or consumables.
- Move
- The cost of moving parts either from stock to the first Production Operation or from one Production Operation to the next.
- Queue
- The cost incurred in waiting for parts to be ready e.g. waiting for paint to dry or heated parts to cool. Queue time is also known as non-instant availability.
If you are using the Fixed Time option (below), these four fields (Labour Cost Item, Setup Cost Item, Move Cost Item and Queue Cost Item) allow you to record these costs when completing a Production Operation. In this case, you need to specify an Item in each of these four fields. Each Item must be a Service Item. Each time you create a Production Operation, it will contain four extra rows: one for each of these Items. These rows allow you to record the various running costs incurred by the Production Operation. The In Qty in each of these rows (number of hours) will be taken from the Routing specified in the Production or from the Standard Operation record specified in the Routing. The Unit Cost will be the Work Cost per Hour (below).
- If you are using the Actual Time option (below), you only need specify a Labour Cost Item. Again, this should be a Service Item. You will record the labour time required for the Production Operation first by creating Activities using the 'Create Activity' function on the Operations menu of the Production Operation. This Item will appear in the Item field of all Activities created in this way. You will then bring these Activities into the Production Operation using the 'Add Labour' function on the same menu. The 'Add Labour' function will add an extra row containing the Labour Cost Item to the Production Operation. The In Qty of this row (number of hours) will be the total Cost (Time) of these Activities (providing they have been marked as Done), and the Unit Cost will be the Work Cost per Hour (below).
- In both cases (Fixed Time and Actual Time), when you mark a Production Operation as Finished, the choice of the Account(s) that will be credited with these running costs will depend on whether you are using the Use Item Groups for Cost Accounts option in the Cost Accounting setting in the Stock module. If you are, and you specify Items in these four fields that belong to Item Groups in which you have specified Production W-cost Accounts, those Accounts will be used. If you are not using this option or the Item Groups do not have Production W-cost Accounts, the W-cost Account will be taken from the Account Usage Stock setting.
- These Items must all be Service Items.
- Run Time Act. Type
- Paste Special
Activity Types setting, CRM module
- The Production Time Entry interface is a simple interface that allows you to work on a Production while automatically recording Labour and Setup Time. If you are using this interface, when you start work on a Production, an Activity will be created automatically, with the time you started work as the Start Time. This Activity is known as a "Run Time" Activity. When you finish working on the Production, the Run Time Activity will be updated automatically with the time when work stopped, and the Activity will be marked as Done.
- Specify here the Activity Type that you want to be used in each Run Time Activity.
- Setup Act. Type
- Paste Special
Activity Types setting, CRM module
- The Production Time Entry interface is a simple interface that allows you to work on a Production while automatically recording Labour and Setup Time. When you finish working on a Production, you will have the opportunity to enter a Setup Time (e.g. time spent calibrating the Machine or replenishing fluids before starting work on the Production). If you enter a Setup Time and if you are using the Add Work Cost option (below), an Activity will be created automatically to record this time. This Activity is known as a "Setup Activity", and will be marked as Done.
- Specify here the Activity Type that you want to be used in each Setup Activity.
- Time
- Use these options to specify whether you will record actual or fixed time against Production Operations.
- Actual
- Recording actual time against a Production Operation is a two-stage process. You should first create Activities using the 'Create Activity' function on the Operations menu of the Production Operation, and then bringing these Activities into the Production Operation using the 'Add Labour' function on the same menu. This function will add an extra row containing the Labour Cost Item specified above to the Production Operation. The In Qty of this row (number of hours) will be the total Cost (Time) of these Activities (providing they have been marked as Done), and the Unit Cost will be the Work Cost per Hour (below).
- Fixed
- If you are using this option, when you create a Production Operation record from a Production, it will contain extra rows for each of the cost types, using the Labour Cost Item, Setup Cost Item, Move Cost Item and Queue Cost Item specified above. The In Quantities of these rows (number of hours) will be taken from the Routing specified in the Production or from the Standard Operation record specified in the Routing. The Unit Cost in each case will be the Work Cost per Hour (below).
- Auto Calculate Cost of produced Items
- Please refer to the description of the Machine Cost Item at the beginning of this page for details of this option.
- Add Work Cost
- This option is used for three purposes.
- First, if you are using the Production Time Entry interface and you want an Activity to be created for Setup Time using the Setup Activity Type specified above, check this box. Run Time Activities will always be created.
- Second, if you are using the Production Time Entry interface together with this option, a Work Cost will be added to each Production automatically. This will be calculated using the total Cost (Time) of the Setup and Run Time Activities and the Work Cost per Hour specified below. Since each Production will be marked as Finished automatically, you will not be able to change this Work Cost. If you have specified a Number Produced in the Recipe, the Cost (Time) of the Setup Activity will be divided by this figure before being added into the calculation.
- Finally, use this option if you would like a Work Cost to be added to each new Recipe automatically. This Work Cost will be calculated using the Work Cost per Hour specified below and the time required for the Recipe (the total of the Time to Setup and the Days, Hours, Minutes and Seconds to Produce). The Work Cost will be placed in the W-cost field in the last Input row in the Recipe. If the Recipe has a Number Produced, this will be used to calculate a Work Cost per unit. You cannot change this calculated Work Cost figure, but you can in effect adjust it by specifying another Work Cost (which can be negative if necessary) in one of the other Input rows. This feature does not apply to Recipes with Routings.
- Work Cost per Hour
- The Work Cost per Hour is used for four purposes.
- First, if you are using the Fixed Time option above, this will be the hourly rate for Labour, Setup Time, Move Time and Queue Time that will be added automatically to Production Operations when you create them from Productions.
- Second, if you are using the Actual Time option above and you use the 'Add Labour' Operations menu function to add time to Production Operations from Activities, this will be the hourly rate.
- Third, if you record time against a Production using the Production Time Entry interface and you are using the Add Work Cost option above, then this time will be added automatically to the Production as a Work Cost using the hourly rate specified here.
- Finally, if you are using the Add Work Cost option above, a Work Cost will be added to each new Recipe automatically. This Work Cost will be calculated using the Work Cost per Hour specified here and the time required for the Recipe (the total of the Time to Setup and the Days, Hours, Minutes and Seconds to Produce). The Work Cost will be placed in the W-cost field in the last Input row in the Recipe. If the Recipe has a Number Produced, this will be used to calculate a Work Cost per unit. This feature does not apply to Recipes with Routings.
- Add Discarded Cost
- If an operative uses the Production Time Entry interface to record that some of what has been produced has been discarded, a second Production will be created for the discarded quantity. This second Production will be marked as Finished but Discarded, thus removing the components from stock and updating the stock valuation in the Nominal Ledger. The two Productions will be connected to each other through the Attachments facility. If you are using this option, the value of the second (Discarded) Production will be added to the first (Finished) Production as a Work Cost, and therefore this value will be included in the stock value of the "good" Items.
---
Settings in the Production module:
Go back to:
|