Entering a Production Operation - Items Card
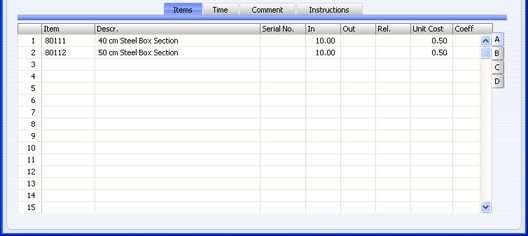
The Items card lists the Input Items that will be used by the Production Operation. When you Finish the Production Operation, these Items will be removed from stock. If the result of the Production Operation is a Phantom or Stocked Item, it will be included in the list as an Output Item. However, it is not necessary for a Production Operation to contain an Output Item.
The function that creates the Production Operation will do so following the instructions in the Routing specified in the parent Production. It will use the Standard Operations listed in the Routing as templates to create Production Operations specific to the Production. From each Standard Operation listed in the Routing, the function will obtain a list of Materials. It will then look in the Production for Input and Output Items with the Materials in the list, and copy these Items to the corresponding Production Operation. If an Input Item in the Production has a Recipe (i.e. the Input Item is a sub-assembly), the function will also look in that Recipe for the relevant Materials and copy any such Items to the relevant Production Operation.
In a particular Production Operation, you are free to add or remove Items, or to change quantities.
If you have used the Time options on the 'Cost Items' card of the Production Settings setting to choose that you will record Fixed Time against Production Operations, the list will include four extra rows for each of the cost types, using the Labour Cost Item, Setup Cost Item, Move Cost Item and Queue Cost Item specified in the same setting. The In Quantities of these rows (number of hours) will be taken from the Routing specified in the parent Production or from the Standard Operation record specified in the Routing. The Unit Cost in each case will be the Work Cost per Hour (also specified in the Production Settings setting).
If, however, you have used the Time options in the Production Settings setting to choose that you will record Actual Time against Production Operations, you will record that time using Activities. You will then bring these Activities into the Production Operation using the 'Add Labour' function on the Operations menu. This function will add an extra row containing the Labour Cost Item specified in the Production Settings setting to the Production Operation. The In Qty of this row (number of hours) will be the total Cost (Time) of these Activities (providing they have been marked as Done), and the Unit Cost will be the Work Cost per Hour.
Flip A
- Item
- Paste Special
Item register
- When you create the Production Operation, Items in the parent Production (and in any sub-assembly Recipes) that share a Material with the template Standard Operation will be copied here.
- Descr.
- Item description from the corresponding Production row.
- Serial No.
- Paste Special
Serial Numbers of Items in stock
- In the case of an Input Item, if necessary enter the Serial Number of the Item you use in the assembly process. In the case of an Output Item, enter the Serial Number you give to the assembly.
- You must use separate rows for Items that are Serial Numbered at unit level, each with an In or Out Quantity of one. This allows you to record separate Serial Numbers and enables their correct removal from stock.
- If you have not specified a Location on the 'Comment' card, the 'Paste Special' list will show the Serial Numbers of Items in all Locations, with an indication of the Location in which each Item is stored. However, if you have specified a Location, only those Serial Numbers stored in that Location will be shown.
- By default, if an Input or Output Item uses Serial Numbers, you must specify a Serial Number here before you can Finish the Production Operation. If you do not assign Serial Numbers to Output Items immediately, you should use the No Serial No. on Goods Receipts option in the Stock Settings setting. This will allow you to Finish Production Operations without Output Item Serial Numbers. You will still have to specify Input Item Serial Numbers, but in this case there will be no 'Paste Special' list, and no check will be carried out that the Serial Number you have used is valid (i.e. one that is currently in stock).
- In
- Enter the quantity of each component required to make or build the finished product. Do not enter an In Qty for the assembled Item(s). This quantity must be one if the Input Item is Serial Numbered at unit level.
- When you create a Production Operation from a Production, the In Qty or Out Qty as appropriate will usually be copied from the Production row to the corresponding Production Operation row. However, if you enter a Quantity in the relevant row in the template Standard Operation, this Quantity will be copied to the Production Operation row instead. If the Production row has an In Qty, the Quantity in the Standard Operation row will be copied to the In Qty field in the Production Operation row. Otherwise, it will be copied to the Out Qty field. The Quantity in the Standard Operation row will therefore take priority over the In and Out Quantities in the Production (which themselves will have been taken from the Recipe).
- If you are using the Production Lines hold Actual Qty option in the Production Settings setting, this figure will at first be the quantity of the component required to complete the Production Operation (i.e. to build the Quantity specified in the header). This figure will be recalculated automatically when you enter an Actual Qty in the header, and each time you change this figure. If you are not using the Production Lines hold Actual Qty option, this figure will be the quantity of the component required to complete one application of the Recipe. This figure will therefore remain unchanged when you enter or change the Actual Qty in the header. In both cases, you can change this figure in a particular Production Operation if necessary.
- If a Nominal Ledger Transaction is generated from this Production Operation, its credit amount will be taken from the total Unit Cost of rows with an In Qty (i.e. Input Items).
- Out
- If the Production Operation has an Output Item, this field should contain the quantity of Out Items that can be made from the components listed above. Usually, this will be just one, and it must be one if the Output Item is Serial Numbered at unit level.
- When you create a Production Operation from a Production, the In Qty or Out Qty as appropriate will usually be copied from the Production row to the corresponding Production Operation row. However, if you enter a Quantity in the relevant row in the template Standard Operation, this Quantity will be copied to the Production Operation row instead. If the Production row has an In Qty, the Quantity in the Standard Operation row will be copied to the In Qty field in the Production Operation row. Otherwise, it will be copied to the Out Qty field. The Quantity in the Standard Operation row will therefore take priority over the In and Out Quantities in the Production (which themselves will have been taken from the Recipe).
- If you are using the Production Lines hold Actual Qty option in the Production Settings setting, this figure will be the quantity of the final Item that will be built by the number of applications of the Recipe specified in the Quantity specified in the header. This figure will be recalculated automatically when you enter an Actual Qty in the header and each time you change this figure. If you are not using the Production Lines hold Actual Qty option, this figure will be the quantity of the final Item that will be built by one application of the Recipe. This figure will therefore remain unchanged when you enter of change the Actual Qty in the header. In both cases, you can change this figure in a particular Production Operation if necessary.
- If a Nominal Ledger Transaction is generated from this Production Operation, its debit amount will be taken from the total Unit Cost of rows with an Out Qty (i.e. Output Items).
- Rel.
- Default taken from
Production row
- Relativity. You must use this field if the result of the Production Operation is that more than one Item will be assembled (i.e. there is more than one row in the Production Operation with an Output Item). The Production Operation might produce different Items (with different Item Numbers) or it might produce more than one of the same Item with Serial Numbers. Enter a figure in each row representing an Output Item. When you mark the Production Operation as Finished, the total stock value of the components will be calculated using the appropriate Cost Models. The stock values of the Output Items will then be calculated from that total using the ratio that you enter here.
- The Relativity figures are not percentages but ratios. For example, the total stock value of the Input Items is 103 and there are two Output Items with Relativities of 30 and 60 respectively. The stock value of the first Output Item will be 103 * 30/(30 + 60), and the stock value of the second Output Item will be 103 * 60/(30 + 60). If the Out Qty of the first Output Item is two, then the unit stock value of the first Output Item will be 103 * 30/((2*30) + 60), and the stock value of the second Output Item will be 103 * 60/((2*30) + 60).
- Unit Cost
- The cost value (per unit) of the component or assembled Item. When you first create a Production Operation, the I-cost from the relevant row in the parent Production will be placed here. However, when you change and save the Production Operation for the first time, this figure will be replaced by the Item's unit stock value (if the row contains an Input Item) or by a unit value calculated from the total value of the components (if the row contains an Output Item). This figure will be used in the Nominal Ledger Transaction generated when you mark the Production as Finished or Discarded and save it. If the Input or Output quantity is greater than one, this field will show the average unit stock value.
- If the row contains an Input Item, this figure (i.e. the Item's unit stock value) will be calculated using the Cost Model specified in the relevant Item or Item Group record. If that Cost Model is Default, the Primary Cost Model specified in the Cost Accounting setting will be used.
- If the row contains an Output Item, this figure will usually be the sum of the Unit Costs of the Input Items, taking quantities into account. If there is more than one Output Item, this total will be distributed according to the ratios entered in the Rel. column. This figure will become the new stock value of the Output Item(s), if that Item is a Stocked Item.
- Coeff
- Default taken from
Production row
- The Unit Coefficient of the Item is shown here, taken from the relevant Production row, which in turn takes it from the 'Stock' card of the Item. If you are maintaining stock quantities using different units of measurement, this coefficient is the ratio between those units of measurement.
Flip B
- Objects
- Paste Special
Object, Nominal Ledger/System module
- Default taken from Production row or Item
- You can assign up to 20 Objects, separated by commas, to each row. You might define separate Objects to represent different departments, cost centres or product types. This provides a flexible method of analysis that can be used in Nominal Ledger reports. Usually the Objects specified here will represent the Item.
- These Objects will be taken from the originating Production row. If the originating Production row contains a Phantom Item, one of whose components is in the Production Operation row, then the Objects will be taken from the relevant Item record.
- In any Nominal Ledger Transactions generated from a Production Operation, any Objects specified here will be assigned to the credit posting for the Item (if the Item is an Input Item) or to the debit posting (if it is an Output Item).
- Material
- Paste Special
Materials setting, Production module
- Default taken from Standard Operation row
- The function that creates the Production Operation will do so following the instructions in the Routing specified in the parent Production. It will use the Standard Operations listed in the Routing as templates to create Production Operations specific to the Production. From each Standard Operation listed in the Routing, the function will obtain a list of Materials. It will then look in the Production for Input and Output Items with the Materials in the list, and copy these Items to the corresponding Production Operation. If an Input Item in the Production has a Recipe (i.e. the Input Item is a sub-assembly), the function will also look in that Recipe for the relevant Materials and copy any such Items to the relevant Production Operation. The Material will be shown in this field as confirmation.
Flip D
- FIFO
- This field shows the unit stock value of the Item. It is updated each time you save the Production Operation. The Item's unit stock value is also shown in the Unit Cost field on flip A: please refer to the description of that field above for more details.
- Row FIFO
- This field shows the total stock value of the row, In Qty * Unit Cost (in the case of Input Items) or Out Qty * Unit Cost (in the case of Output Items).
---
In this chapter:
See also:
Go back to:
|